Des revêtements en couches minces pour surmonter les défis des moteurs hydrogène à combustion interne
Par Dr. Astrid Gies (Oerlikon Surface Solutions AG), Dr. Joerg Jorzick et Dr. Timea Stelzig (Oerlikon Balzers Coating Germany Gmbh
Le traitement thermique sous atmosphère est une condition indispensable pour obtenir des produits de haute qualité. Une grande variété de tubes radiants est disponible pour l’équipement des fours sous atmosphère. Parmi les différentes formes de tubes radiants comme les tubes en U, W, P, le tube en doigt de gant est le plus adapté quand l’uniformité de température est une priorité.
Introduction
La Commission européenne a proposé de réduire les émissions de CO2 par étape jusqu’à 90 % à partir de 2040 en référence à la situation de 2019[1]. Les États-Unis, quant à eux, visent une réduction des émissions de CO2 de 47 % à partir de 2027 (comparativement à 2010) avec des régulations encore plus strictes dans certains états comme la Californie[2,3]. Concernant la Chine, les régulations seront également plus strictes, puisque le président de la République populaire de Chine a annoncé en septembre 2020 la réduction des émissions de CO2 à « net-zéro » à partir de 2060.
Afin de réduire les émissions de CO2 à un « net-zéro », il existe quatre technologies principales pour la propulsion des véhicules de poids légers, tout comme pour les poids lourds :
1. Les véhicules électriques à batterie (BEV) ;
2. Les véhicules électriques à piles à combustible (FCEV) ;
3. Les moteurs d’hydrogène à combustion interne (H2-ICE) ;
4. Les moteurs à combustion interne (ICE) utilisant des biocarburants ou encore des carburants synthétiques.
Toutes ces technologies présentent des avantages et des inconvénients, selon le type de véhicule. Concernant les H2-ICEs, l’émission de CO2 peut être réduite à « net-zéro » si de l’hydrogène « vert » (produit en utilisant des énergies renouvelables) est utilisé. En revanche, les moteurs H2-ICE et les moteurs thermiques traditionnels carburés en hydrocarbures émettent toujours des oxydes nitreux (NOx) et alors, un post-traitement des gaz d’échappement s’avère nécessaire.
De plus, le problème de la faible efficacité globale des moteurs à combustion interne par rapport aux véhicules BEV ou FCEV demeure lorsque l’hydrogène est utilisé comme carburant. Néanmoins, l’efficacité des moteurs H2-ICE étant meilleure sous charge élevée, ces derniers sont plus appropriés à l’application aux poids lourds que le sont les moteurs ICE traditionnels ou encore les FCEV.
Pour les véhicules passagers ou de poids légers, l’électrification de la propulsion, soit par batterie électrique, soit par pile à combustible, semble actuellement la solution la plus favorable. Néanmoins, cela s’avère beaucoup plus difficile pour les engins opérants sous fortes charges et à longues portées comme les poids lourds, mais aussi pour les engins du secteur marin et de l’aéronautique. C’est pourquoi de grands efforts sont entrepris par les différents acteurs du marché pour développer des moteurs H2-ICE. Ces derniers permettraient de continuer à utiliser une technologie de propulsion mature tout en utilisant un carburant n’émettant pas de CO2, sous condition que l’hydrogène soit produit à base d’énergies renouvelables. En outre, le développement des installations nécessaires pour le stockage et la distribution de l’hydrogène pourrait aussi promouvoir l’emploi des piles à combustible, sachant que ces dernières demandent une qualité d’hydrogène plus élevée que les moteurs thermiques.
L’usure de l’hydrogène en tant que carburant
Par sa nature chimique, l’hydrogène possède des propriétés uniques comparé aux combustibles fossiles comme le diesel, l’essence ou encore le GNC. L’hydrogène ne contient pas de carbone, il est donc de fait une alternative « net-zéro » en émissions de CO2 par rapport aux hydrocarbures.
Il possède une densité d’énergie spécifique très élevée, de l’ordre de 120 MJ/kg, et délivre environ trois fois plus d’énergie par masse que les hydrocarbures conventionnels. La température d’auto-allumage de l’hydrogène est d’environ 585 °C, donc bien supérieure à celle des combustibles fossiles permettant aux moteurs H2-ICE d’être opérés à des régimes de compression plus élevés. Le RON (« Research Octane Number ») de l’hydrogène étant relativement important (≥ 130), l’efficacité thermique (« BrakeThermal Efficiency ») des moteurs H2-ICE est supérieure à celle des moteurs thermiques classiques.
En revanche, l’hydrogène possède une faible densité, ce qui augmente considérablement l’espace requis pour le stockage. Cela constitue un inconvénient, surtout pour les véhicules particuliers, mais aussi pour les poids lourds[4-6].
Lors de la conversion d’un moteur thermique classique en H2-ICE, plusieurs défis apparaissent et peuvent impliquer une modification de certains composants du moteur. L’un des inconvénients de l’hydrogène est sa faible énergie minimum d’allumage en air (0.02 MJ comparé à 0.24 MJ pour le pétrole). Le mélange hydrogène/air peut donc plus facilement s’auto-allumer lorsqu’il entre en contact avec des surfaces chaudes dans le cylindre ; ce qui provoque des effets indésirables comme le « cognement » du moteur ou encore l’allumage prématuré lors de l’injection de l’hydrogène[7].
De plus, et contrairement aux hydrocarbures, l’hydrogène n’a pas ou très peu d’effet lubrifiant au sein des contacts tribologiques. Cela est dû à sa nature gazeuse et à sa combustion relativement propre conduisant à une très faible formation de résidus (coke de pétrole), donc de « troisième corps » par rapport à la combustion des hydrocarbures [8]. L’hydrogène étant le plus petit des éléments chimiques, il diffuse facilement dans d’autres matériaux. Lorsque l’hydrogène diffuse dans l’acier, les propriétés mécaniques de ce dernier, comme sa résistance à la fatigue, sont parfois sévèrement affectées. Cette fragilisation par l’hydrogène (« Hydrogen Embrittlement ») du matériau se traduit par une réduction de la ténacité à la rupture, conduisant à la formation de fissures et à une usure prématurée voire à la défaillance complète du composant[9, 10].
La température de la combustion de l’hydrogène est plus élevée que celle des hydrocarbures, ce qui peut nécessiter une protection thermique de certains composants du moteur. En outre, l’hydrogène est chimiquement corrosif pour les élastomères et peut entraîner un endommagement des joints dans le moteur.
Pour résumer, les défis suivants, liés à l’utilisation de l’hydrogène dans les moteurs thermiques, sont clairement identifiés. L’application de certains revêtements sous forme de couches minces peut être une solution pour surmonter au moins quelques-uns de ces défis, notamment les trois premiers :
1. pas ou très peu d’effet lubrifiant de l’hydrogène sur les contacts tribologiques ;
2. température plus élevée de la combustion de l’hydrogène conduisant à une sollicitation thermique plus importante de certains composants du moteur ;
3. fragilisation par l’hydrogène des composants en acier et usure prématurée des joints ;
4. maîtrise de la combustion de l’hydrogène afin d’éviter le cognement de moteur ou un auto-allumage prématuré ;
5. gestion des problématiques associées à la formation de l’eau lors de la combustion de l’hydrogène.
Les revêtements, des solutions potentielles
1. Manque de lubrification
Comme indiqué plus haut, l’hydrogène n’a pas ou très peu d’effet lubrifiant sur un contact tribologique. C’est pourquoi certains revêtements ayant de faibles coefficients de frottement avec l’acier dans un contact non-lubrifié peuvent être employés. Les revêtements de type DLC (« Diamond Like Carbon ») sont utilisés depuis plus de 20 ans en grande série par l’industrie automobile, mais aussi dans d’autres secteurs pour leurs propriétés uniques en termes de faible coefficient de frottement (0.1-0.2 avec acier, non-lubrifié) et de résistance à l’usure importante[11-14]. Les revêtements DLC représentent une large gamme de différents types de dépôts (figure 1), classifiés selon la norme allemande VDI 2840[15].
Ces revêtements sont typiquement déposés par des technologies PVD (dépôts physiques en phase vapeur) ou PACVD (dépôts chimiques en phase vapeur, assistés plasma). Selon la composition chimique (hydrogénée ou pas, dopée ou pas aux éléments métalliques ou non-métalliques) et la nature des liaisons chimiques des atomes de carbone dans le matériau (faible ou forte teneur en carbone tétraédrique sp3), une large gamme de propriétés peut être obtenue. La dureté de ces revêtement peut aller de 12-15 GPa pour les a-C:H:Me (carbone amorphe hydrogéné et dopé en métal) à 60GPa et plus pour les ta-C (carbone amorphe tétraédrique non-hydrogéné) en passant par 18-25 GPa pour les a-C:H (carbone amorphe hydrogéné non-dopé).
Les revêtements DLC de type a-C:H sont utilisés depuis des années dans les injecteurs de diesel (et plus récemment dans les injecteurs d’essence) afin d’augmenter la résistance à l’usure de ces pièces lorsqu’elles opèrent à de très hautes pressions, de l’ordre de 2 000 bars et plus pour l’injection du diesel. Néanmoins, la stabilité thermique de ce matériau est limitée à environ 350 °C et moins en fonction de la pression de contact[16, 17].
Les revêtements a-C:H ne sont donc pas les dépôts DLC les plus adaptés à l’injection d’hydrogène par rapport à la température plus élevée attendue pour les moteurs H2-ICE. Les revêtements DLC non-hydrogénés de type a-C et ta-C ont pour avantage une meilleure stabilité thermique (450-500 °C) tout en gardant un faible coefficient de frottement avec l’acier dans un contact sec non-lubrifié.
C’est pourquoi ces derniers revêtements sont proposés, ces derniers temps, comme solution potentielle pour la réduction du frottement et l’augmentation de la résistance à l’usure de certains composants des moteurs H2-ICE.
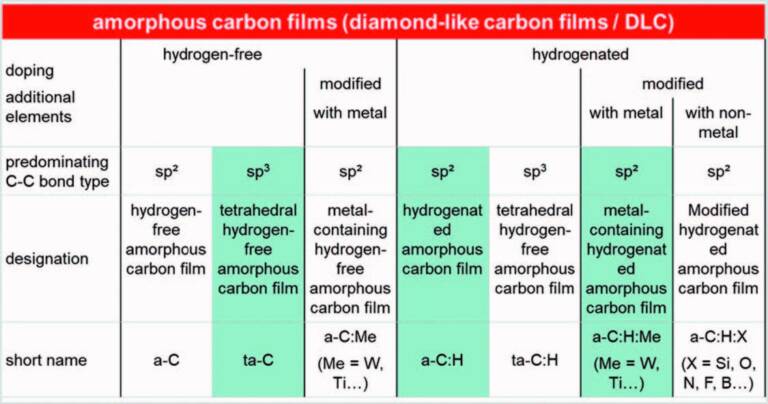
Figure 1 : Classification des revêtements DLC selon la norme allemande VDI 2840[15]
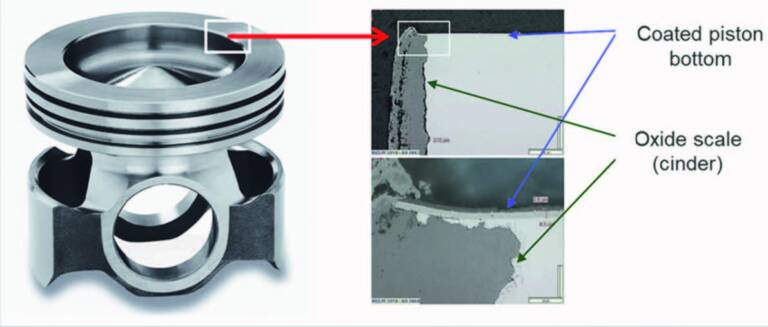
Figure 2 : Images MEB (coupe transversale) d’un piston revêtu en AlCrO après un recuit à 600°C pour 3 000 heures en atmosphère ambiante (courtoisie Dr. R. Rose, Mahle GmbH, Stuttgart, Allemagne)
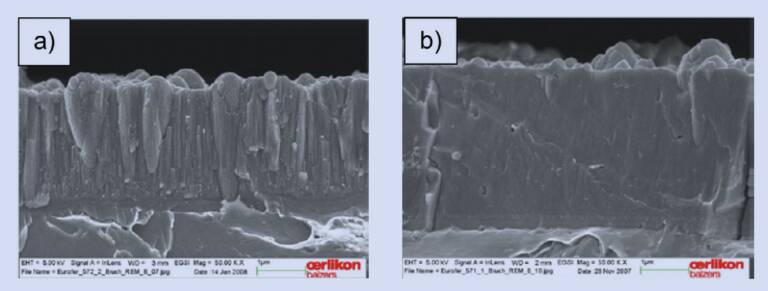
Figure 3 : Images MEB (coupe transversale) de deux revêtements AlCrO déposés par évaporation par arc avec un flux d’oxygène faible (a) et élevé (b) lors du dépôt
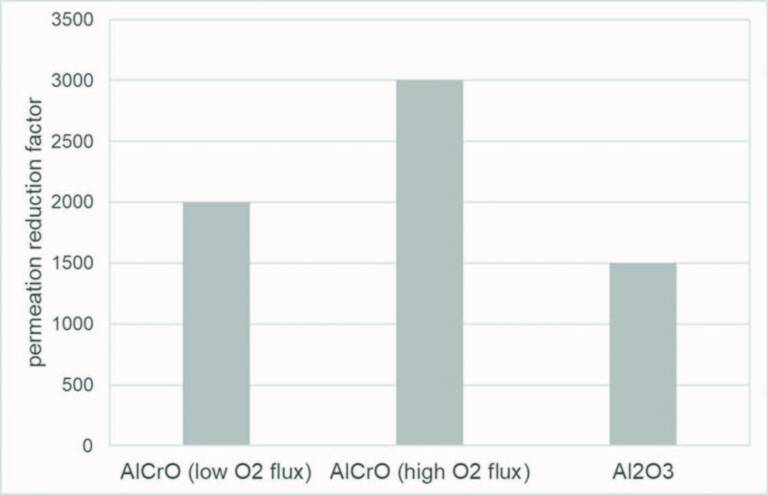
Figure 4 : Pouvoir réducteur à la perméation d’hydrogène d’un substrat d’acier (EUROFER 97) revêtu en AlCrO (flux d’oxygène faible et élevé). Le résultat obtenu pour un dépôt d’alumine (1µm, dépose à 720°C) est donné pour comparaison.
Bibliographie
[1] “European Green Deal: Commission proposes 2030 zero-emissions target for new city buses and 90% emissions reductions for new trucks by 2040”, press release 14.02.2023, European Commission, https://ec.europa.eu/commission/presscorner/detail/en/ip_23_762
[2] “Greenhouse gas emissions and fuel efficiency standards for medium- and heavy-duty engines and vehicles”, Federal Register 15.09.2011, https://www.govinfo.gov/app/details/FR-2011-09-15/2011-20740
[3] “Greenhouse gas emissions and fuel efficiency standards for medium- and heavy-duty engines and vehicles - phase 2”, Federal Register 25.10.2016, https://www.govinfo.gov/app/details/FR-2016-10-25/2016-21203
[4] “A review of hydrogen direct injection for internal combustion engines: towards carbon-free combustion”, H.L. Yip et al., Appl. Sci. 9 (2019)
[5] “Hydrogen fueled internal combustion engine : a review”, M.A. Ahmed, Int. J. Innovative Technology & Research 4 (2016)
[6] “Hydrogen-fueled internal combustion engine : a review of technical feasibility”, S.K. Sharma et al., Int. J. Performability Engineering 11 (2015)
[7] “The hydrogen-fueled internal combustion engine : A technical review”, C.M. White et al., Int. J. Hydrogen Energy 31 (2006)
[8] “A comprehensive overview of hydrogen-fueled internal combustion engines: achievements and future challenges”, Z. Stepién, Energies 14 (2021)
[9] “Hydrogen embrittlement and fatigue fracture of a crankshaft of an internal combustion engine”, G. Zucca et al., Procedia Engineering 109 (2015)
[10] “Hydrogen permeation barriers and preparation techniques: a review”, S. Xiao et al., J. Vacuum Science & Technology A 40 (2022)
[11] “Diamond-like amorphous carbon”, J. Robertson, Materials Science and Engineering R 37 (2002)
[12] “Tribology of diamond-like carbon films: recent progress and future prospects”, A. Erdemir et al., J. of Physics D: Applied Physics 39 (2006)
[13] “Wear Resistance of Amorphous DLC and Metal Containing DLC in Industrial Applications”, G.J. van der Kolk, in Tribology of Diamond-Like Carbon Films: Fundamentals and Applications, Donnet, C., Erdemir, A. (eds.) New York, Springer Science + Business Media (2008)
[14] “Evaluation of DLC coatings for spark-ignited, direct-injected fuel systems”, J. Hershberger et al., Surface and Coatings Technology 179 (2004)
[15] German Guideline VDI 2840 : Carbon films – Fundamentals, film types and properties
[16] “Thermal effects influencing stability and performance of coatings in automotive applications”, J. Becker et al., Surface and Coatings Technology 284 (2015)
[17] “The graphitization of the hydrogenated DLC film structure”, H. Ronkainen et al., in Tribology of Diamond-Like Carbon Films: Fundamentals and Applications, Donnet, C., Erdemir, A. (eds.) New York, Springer Science + Business Media (2008)
[18] “Hydrogen permeability of diamondlike amorphous carbons”, M. Tamura et al., J. of Vacuum Science
& Technology A 135 (2017)
[19] “The role of surface oxidation in friction processes on molybdenum nitride thin films”, T. Suszko et al., Surface and Coatings Technology 194 (2005).
[20] “Thermal stability of arc evaporated Al-Cr-O and
Al-Cr-O/Al-Cr-N multilayer coatings”, R. Raab et al., Surface and Coatings Technology 352 (2018)
[21] “On the oxidation behaviour of cathodic arc evaporated Al-Cr and Al-Cr-O coatings”, V. Dalbauer et al., Vacuum 163 (2019)
[22] “Tritium Diffusion in A12O3 and BeO”, J.D. Fowler
et al., J. American Ceramic Society 60 (1977)
[23] “Al–Cr–O thin films as an efficient hydrogen barrier”, D. Levchuk et al., Surface and Coatings Technology 202 (2008)
Quant à la diffusion de l’hydrogène dans le matériau, il a été démontré l’intérêt des revêtements de type a-C:H[18]. En effet, les dépôts a-C:H avec une teneur en hydrogène de 20 % ont montré une performance prometteuse en tant que barrière à la diffusion de l’hydrogène dans des tests à l’échelle laboratoire. Il semble que l’effet de barrière à la diffusion de l’hydrogène des revêtements DLC non-hydrogénés (a-C et ta-C) pourrait être limité.
2. Température élevée de la combustion d’hydrogène
La température de la combustion de l’hydrogène étant plus élevée que celle des hydrocarbures, il devient encore plus nécessaire de protéger les surfaces dans le moteur de l’impact thermique, comme les pistons. Comme la stabilité thermique des revêtements DLC est limitée, ces derniers ne conviennent pas aux exigences de tous les composants des moteurs H2-ICE.
Il faut donc s’orienter vers d’autres types de revêtements comme les oxydes (par exemple AlCrO) ou une combinaison d’oxydes et de nitrures (par exemple un système de multicouches AlCrO/AlCrN) ou encore les oxynitrures (par exemple AlCrON). Ces matériaux possèdent en général une très bonne stabilité thermique et une excellente tenue à l’oxydation[20, 21]. Lorsque ces matériaux sont déposés sur un substrat d’acier, une fine couche d’interface comme le CrN est utilisée comme interface entre l’acier et le revêtement fonctionnel. Cette couche d’interface a pour but d’assurer une douce transition des propriétés mécaniques entre l’acier et le revêtement fonctionnel et d’accommoder les différents coefficients de dilatation thermique des deux matériaux.
Ces revêtements mentionnés ci-dessus ont démontré leur capabilité en tant que barrière d’oxydation et sont aujourd’hui utilisés en grande série dans des moteurs thermiques, notamment dans des applications de sport automobile, afin de protéger les pistons contre l’impact thermique et l’oxydation à chaud (figure 3).
3. Fragilisation par hydrogène
Comme déjà mentionné, l’hydrogène, par sa petite taille, diffuse facilement dans des matériaux comme l’acier tout en détériorant ses propriétés mécaniques, ce qui doit être pris en compte pour les moteurs H2-ICE. C’est pourquoi il devient crucial de protéger les surfaces métalliques dans le moteur contre sa diffusion. Une solution consiste à appliquer une barrière à la diffusion d’hydrogène sur le matériau métallique de base afin d’éviter ou de retarder la diffusion d’hydrogène dans le matériau. Ce concept a été proposé il y a une cinquantaine d’années déjà. Depuis, de nombreuses études ont visé à développer des barrières de diffusion d’hydrogène efficaces[22].
Un tel matériau doit comporter aussi peu de défauts que possible (fissures, pores). De plus, il est impératif de choisir un matériau présentant une faible solubilité, un moindre coefficient de diffusion et une faible perméabilité vis-à-vis de l’hydrogène.
Ces dernières décennies différents revêtements ont été développés, y compris des céramiques (nitrures, oxydes, carbures), des métalliques, des matériaux 2D (graphène) et des combinaisons de différents types de matériaux[10].
Oerlikon Balzers a étudié le potentiel d’un revêtement AlCrO en tant que barrière à la diffusion d’hydrogène[23]. Ce revêtement a été déposé par évaporation par arc cathodique avec une épaisseur d’environ 2 µm [Fig. 3]. Selon les paramètres de dépôt, un revêtement dense démontrant une très bonne stabilité thermique peut être obtenu.
Le potentiel de ce revêtement en tant que barrière à la diffusion d’hydrogène a été étudié dans des tests de perméabilité d’hydrogène en laboratoire. Le pouvoir réducteur à la perméation d’hydrogène de ce matériau, selon les paramètres de dépôt, est de 2 000 à 3 000 fois plus élevé par rapport au matériau de base non-revêtu et aussi plus élevé par rapport à un dépôt d’alumine (figure 4).
Conclusion
Actuellement, des efforts sont entrepris afin de développer des moteurs H2-ICE comme alternative « net-zéro » CO2 aux moteurs thermiques à hydrocarbures. Néanmoins, la conversion d’un moteur thermique traditionnel en H2-ICE engendre des défis liés aux propriétés uniques de l’hydrogène dont certains peuvent être relevés en utilisant des revêtements déposés sous forme de couches minces. Les revêtements à base de carbone amorphe (DLC) avec leur faible coefficient de frottement avec l’acier et leur résistance élevée à l’usure peuvent, en partie, compenser le faible pouvoir lubrifiant de l’hydrogène. Des revêtements à base d’oxydes ou de nitrures peuvent protéger efficacement les surfaces métalliques d’un moteur contre l’oxydation ou encore la diffusion d’hydrogène dans le matériau de base.
De nos jours, plusieurs études sont menées visant à améliorer soit la stabilité thermique des revêtements soit le renfort de leur efficacité en tant que barrière à la diffusion d’hydrogène. Très peu d’études sont entreprises pour combiner les deux. Prenant en compte les sollicitations tribologiques dans un moteur à combustion interne, aucune solution n’existe à ce jour. C’est dû notamment à un manque d’équipements adéquats à l’échelle du laboratoire (température, pression d’hydrogène et sollicitations tribologiques), proche de l’application réelle. C’est pourquoi trouver des revêtements adaptés aux moteurs H2-ICE est toujours un défi et des solutions sur mesure seront requises à l’avenir.