Nouvelle chimie de nickel sans acide borique
Par Damien Comte, équipe Global Plating Enginnering, Amphenol, Communications Solution
Amphenol est une société spécialisée dans la fabrication de connecteurs électriques. Ceux-ci permettent de relier électriquement deux éléments d’un circuit mécaniquement dissociable. La division Communications Solutions (CS) développe et fabrique des connecteurs pour les marchés des communications, des produits mobiles grand public, des RF, de l’optique, du haut débit et de l’électronique commerciale. Les connecteurs sont généralement fabriqués à partir d’un substrat cuivreux (laiton ou bronze), recouvert d’une ou plusieurs couches métalliques permettant de leur conférer les propriétés souhaitées (conduction électrique, résistance à l’usure, à la corrosion) selon l’application visée.
Dans le domaine de la connectique électronique, les connecteurs sont plaqués au défilé (reel-to-reel), la bande de substrat passant successivement et sans interruption dans les différents bains de placage galvanique (Cf. figure A).
À la sortie des lignes de production, Amphenol obtient donc les différentes couches métalliques déposées aux endroits voulus. Le plus souvent, et comme présenté ci-dessous sur une bande de contact AirmaxVS©, des métaux précieux dans les zones de contact électrique, de l’étain dans la zone de soudure. Pour la quasi-totalité des connecteurs, la première couche plaquée est une couche de nickel d’une épaisseur de 1 à 2 µm. Cette couche assure deux rôles essentiels pour le connecteur : celui de couche anti-corrosion et celui de barrière de diffusion entre le substrat et les métaux précieux déposés ensuite (Cf. figure B).
Historiquement, dans la connectique, le nickel est déposé à partir de solutions de sulfamate de nickel qui permettent d’obtenir des vitesses de dépôt élevées et une bonne ductilité du nickel déposé. Des solutions à base de sulfate de nickel sont aussi fréquemment en place.
Différents additifs organiques dans ces solutions permettent d’adapter les propriétés (visuelles, ductilité, corrosion) des couches de nickel obtenues. Un élément commun à toutes les chimies de nickel en place est l’utilisation de l’acide borique comme solution tampon pour la stabilité des bains.
L’acide borique est un composé chimique couramment utilisé pour stabiliser le pH des solutions aqueuses acides. Il permet effectivement de maintenir le pH entre 3 et 5 en compensant la perte de protons qui se produit pendant l’électrodéposition des espèces métalliques, dans ce cas le nickel.
Il est à noter que nous développerons ici l’étude sur les chimies de nickel pur, mais que l’acide borique est aussi utilisé dans bien d’autres chimies de dépôt d’alliages de nickel et de beaucoup d’autres métaux.
Bien que l’acide borique a fait ses preuves en termes de performances techniques, deux problèmes majeurs incitent le service de R&D (et les fournisseurs de chimie) à rechercher, tester et valider des alternatives présentant les mêmes performances techniques :
le premier problème concerne la dangerosité pour la santé et la réglementation en vigueur. Depuis le 18 juin 2010, la commercialisation et l’utilisation de l’acide borique sont réglementées en Europe, en raison de sa présence sur la liste candidate à l’annexe XIV du règlement REACH et de sa classification en tant que produit CMR (cancérigène, mutagène, reprotoxique). Le 12 avril 2023, la 11e recommandation de l’ECHA à la commission européenne a demandé l’ajout de l’acide borique et ses dérivés à la liste des substances soumises à autorisation (annexe XIV) ;
le second problème concerne le stockage et la solubilité de l’acide borique. À une température de 30 °C, l’acide borique est soluble dans l’eau jusque 66 g/L, cette limite de solubilité tombe à seulement 50.4 g/L à 20 °C et à 10 °C, seulement 35,7 g d’acide borique sont solubles dans 1 L d’eau.
Dans les bains de nickel fréquemment utilisés dans l’industrie, l’acide borique est concentré autour de 60 g/L. Cela a donc un impact écologique et économique, car il est nécessaire de maintenir la température des bains au minimum à ~ 30 °C lors du stockage ou de l’arrêt des lignes de traitement de surface afin d’éviter la cristallisation de l’acide borique dans le bain, et donc l’obstruction des filtres, pompes, tuyaux, etc.
Nous avons donc lancé une étude afin de mieux comprendre les possibilités de remplacement de l’acide borique dans un bain de nickel, d’évaluer les performances techniques d’un nouvel additif proposé par un de nos fournisseurs et d’établir l’influence de différents paramètres sur l’aspect, les vitesses de dépôts, les propriétés mécaniques et la résistance à la corrosion du dépôt de nickel obtenu.
I. État de l’art
Comme indiqué plus haut, l’utilisation de l’acide borique dans les bains de dépôt de nickel est courante depuis de nombreuses années en raison de ses propriétés tampon et de sa capacité à améliorer la ductilité et la résistance à la corrosion du nickel. Cependant, en raison des inquiétudes environnementales liées à l’utilisation de l’acide borique, plusieurs études ont été menées ces dernières années pour trouver des alternatives plus écologiques.
Une étude, menée par Zhao et Al. en 2016, a montré que l’utilisation d’une solution de chlorure de sodium comme agent tampon dans le bain de nickel conduisait à des revêtements présentant des propriétés similaires à ceux obtenus avec de l’acide borique. Les chercheurs ont également montré que cette solution était plus respectueuse de l’environnement que l’acide borique.
Une autre étude, menée par Gao et Al. en 2017, a évalué l’effet de différentes solutions tampons à base d’acides organiques, telles que l’acide citrique et l’acide tartrique, sur les propriétés des dépôts de nickel. Les résultats ont montré que l’acide tartrique était le plus efficace pour produire des revêtements de nickel ayant des propriétés mécaniques et de corrosion, similaires à ceux obtenus avec de l’acide borique.
En 2018, Zhang et Al. ont étudié l’efficacité d’une solution tampon à base de carbonate de sodium pour le dépôt de nickel. Les chercheurs ont constaté que cette solution tampon permettait d’obtenir des dépôts de nickel présentant des propriétés similaires à ceux obtenus avec de l’acide borique. De plus, la solution tampon à base de carbonate de sodium était également plus respectueuse de l’environnement que l’acide borique.
Enfin, en 2019, Tian et Al. ont évalué l’efficacité d’une solution tampon à base d’acétate de sodium pour le dépôt de nickel. Les résultats ont montré que cette solution tampon était efficace pour produire des revêtements de nickel ayant des propriétés mécaniques et de corrosion, similaires à ceux obtenus avec de l’acide borique.
Globalement toutes ces études ont montré que l’utilisation d’alternatives à l’acide borique comme agent tampon dans les dépôts de nickel est possible tout en produisant des revêtements ayant des propriétés similaires, voire améliorées dans certains cas. En outre, ces alternatives sont également plus respectueuses de l’environnement.
Dans ce contexte, il est intéressant d’étudier la formulation d’un bain de nickel avec un autre agent tampon fourni par un de nos formulateurs de chimie pour évaluer les propriétés des dépôts obtenus. Cette étude contribue ainsi à la recherche sur le développement de revêtements de nickel à partir de solutions plus respectueuses de l’environnement.
Ce projet comporte de nombreuses incertitudes techniques, notamment en ce qui concerne l’impact du nouvel additif sur les performances du nickel puisque cela peut avoir un impact direct sur la fiabilité et la durabilité de nos connecteurs. Même si l’acide borique n’est pas encore officiellement banni – ni même en passe de l’être à court terme – il est impératif d’avancer dans ce projet et d’approfondir nos connaissances sur les performances du nouveau bain de revêtement de nickel sans acide borique afin de valider si nous avons d’ores et déjà une solution de remplacement efficace permettant de garantir une utilisation sûre et fiable de nos connecteurs dans différents secteurs industriels.
À ce stade, nous devons lever les incertitudes techniques suivantes :
la maîtrise des paramètres opératoires tels que la vitesse de dépôt, les densités de courant à mettre en œuvre et la fluidique est cruciale pour garantir des propriétés homogènes et reproductibles du revêtement de nickel ;
la caractérisation des propriétés mécaniques de ce nouveau revêtement, notamment en termes d’élasticité et d’élongation, est essentielle pour évaluer sa résistance aux contraintes mécaniques et sa durabilité dans les applications industrielles ;
la compréhension de l’impact de ce nouvel additif sur les propriétés de résistance à la corrosion est également un aspect crucial de ce projet. Il est important de s’assurer que le nouveau revêtement offre une protection adéquate contre la corrosion, qui est un facteur clé de la fiabilité des connecteurs ;
enfin, il est important de caractériser l’impact de ce nouvel additif sur la cristallographie et la taille des cristallites des revêtements de nickel. Cette connaissance est essentielle pour comprendre la structure et la composition du revêtement, ce qui est important pour sa performance globale et sa durabilité.
II. Déroulement des essais – Résultats obtenus
Afin d’étudier l’impact de ce nouvel additif sur l’aspect du revêtement, nous avons commencé par réaliser 6 cellules de Hull avec des courants appliqués différents : 3 avec la chimie standard et 3 avec la nouvelle formulation. La figure 1 illustre les 6 cellules de Hull obtenues, celles à partir de la formulation standard se retrouvent en bleu en haut, et celles à partir de la nouvelle formulation sans acide borique se retrouvent en bas en rouge.
Les résultats de cette étude comparative montrent qu’il n’y a pas de différence significative d’aspect entre les revêtements de nickel obtenus, à l’exception de la couleur et de la texture du revêtement brûlé. Lorsque le dépôt est brûlé, le revêtement obtenu à partir du bain sans acide borique est beaucoup plus noir et pulvérulent que celui obtenu avec acide borique. Toutefois, en termes de plage de travail, les deux bains testés atteignent une zone de brûlure à des densités de courant similaires.
La morphologie des dépôts de nickel a également été observée par microscope électronique à balayage (MEB). Elles sont très similaires pour les deux formulations.
Cela suggère que l’acide borique n’est pas indispensable pour la formation d’un revêtement de qualité, mais qu’il peut affecter la couleur et la texture du revêtement brûlé. Il convient toutefois de noter que ces résultats peuvent varier en fonction des conditions spécifiques de chaque processus de fabrication.
Pour étudier la vitesse de placage des deux chimies et ainsi pouvoir les comparer, les épaisseurs des dépôts de nickel en fonction de la densité de courant pour les 6 cellules de Hull ont été mesurées. Pour ce faire, nous avons utilisé la fluorescence des rayons X (XRF). Cette technique permet, après une calibration adaptée, de mesurer l’épaisseur des dépôts de manière non destructive.
La figure 2 montre les résultats obtenus, en bleu pour le nickel standard et en rouge pour le nickel sans acide borique.
D’après ces résultats, les épaisseurs des dépôts de nickel obtenus à partir des deux bains testés sont similaires. Ces observations indiquent que le remplacement de l’acide borique par ce nouvel agent tampon n’affecte pas la vitesse de placage du nickel, celle-ci est comprise entre 1,7 et 2,0 µm/min à une densité de courant de 10 ASD et entre 3,0 et 3,5 µm/min à une densité de courant de 20 ASD, pour les deux formulations.
Afin d’étudier l’impact du pH sur la vitesse de placage, 6 panneaux de Hull ont été plaqués à 3 pH différents. Les résultats obtenus sont regroupés dans la figure 3, avec un pH de 2,8, soit en bas de la gamme de traitement recommandée (en bleu), de 3,2 en milieu de gamme (en vert) et un en haut de la gamme à 3,8 (en rouge). En utilisant la fluorescence des rayons X (XRF), des mesures d’épaisseur ont été effectuées à différentes densités de courant pour les 6 panneaux de Hull.
La vitesse de placage est équivalente pour les deux formulations testées ainsi que pour les 3 valeurs de pH étudiées.
La vitesse de placage est d’environ
1,8 µm/min à une densité de courant de 10 ASD et entre 3,0 et 3,4 µm/min à une densité de courant de 20 ASD.
Nous avons même fait des essais sur une plage de pH plus large, entre 1,8 et 4,7, montrant là encore des comportements très similaires entre ces deux formulations.
Les résultats de cette étude montrent qu’il n’y a pas d’impact significatif du changement d’agent tampon ou de la variation du pH dans la plage de traitement recommandée sur la vitesse de placage du nickel. Ainsi, nous pouvons conclure que cette formulation de nickel sans acide borique peut être considérée comme une alternative efficace pour la production de revêtements de nickel, sans affecter significativement la vitesse de placage. Nous avons également étudié les propriétés mécaniques des revêtements obtenus avec et sans l’agent tampon d’acide borique. Plus précisément, nous avons réalisé des tests de nano-indentation pour évaluer la dureté et le module de Young des revêtements. Les tests ont été effectués à des densités de courant de 5, 10, 20 et 30 ASD. La force normale appliquée pour ces tests était de 2 mN.
Ces résultats montrent que la densité de courant a une influence sur les propriétés mécaniques des revêtements de nickel, quelle que soit la formulation. Comme le montrent les résultats illustrés dans la figure 4, une augmentation de la densité de courant entraîne effectivement une augmentation de la dureté des dépôts obtenus par les deux formulations, ce qui peut être lié à une augmentation de la compacité du dépôt.
Cependant, il est intéressant de noter que le module de Young (figure 5), qui mesure la rigidité du matériau, ne suit pas la même tendance pour les deux formulations. Pour le nickel standard, le module de Young augmente avec la densité de courant, tandis qu’il diminue pour le nickel sans acide borique. Ces résultats soulignent l’impact de ce nouvel agent tampon sur la rigidité finale du revêtement pour de fortes densités de courant.
Afin d’évaluer l’élasticité des revêtements, des tests de pliage ont été réalisés avec différents pourcentages d’élongation, variant de 17 à 32 %, sur des échantillons déposés à 3 densités de courants différentes 5, 10 et 20 ASD. Ensuite, dans le but de caractériser et de quantifier les résultats obtenus, la profondeur moyenne des fissures a été mesurée à l’aide d’un profilomètre optique et du logiciel Vision64. Les résultats obtenus sont illustrés dans la figure 6.
Ces graphiques montrent que la profondeur moyenne de fissuration des revêtements augmente en fonction de la densité de courant et du pourcentage d’élongation, et ce pour les deux formulations. Cette augmentation se fait plutôt de façon « exponentielle » pour le nickel standard, tandis que pour le nickel sans acide borique, elle est plutôt « linéaire ».
Les résultats ont également montré que pour les faibles élongations, le nickel standard présente des profondeurs moyennes de fissuration plus petites que le nickel sans acide borique. Cependant, à 32 % d’élongation, les meilleurs résultats ont été obtenus avec la formulation sans acide borique. Dans le but d’étudier le comportement tribologique des deux dépôts et d’établir si le changement d’agent tampon du bain de nickel a un impact, des tests de fretting ont également été réalisés. Les tests de fretting, pendant lesquels des échantillons sont soumis à des déplacements de faible amplitude à quelques Hertz de fréquence, sont très répandus en connectique. Ils permettent de simuler au laboratoire les contraintes en vibration subies par le connecteur en fonctionnement. Les deux sous-couches de nickel ont été revêtues par une couche de palladium-nickel de 0,6 µm, suivie d’un flash d’or de 50 nm. Les multicouches GXT© (Au/PdNi/Ni) ainsi obtenus ont été soumis à des tests de fretting dans les conditions suivantes : 50 µm de déplacement, une fréquence de 10 Hz et une charge normale de 1 N. La figure 7 montre l’évolution de la résistance de contact en fonction des cycles de fretting avec la formulation sans acide borique en bleu et avec acide borique en vert. La figure 8 montre l’évolution du coefficient de frottement avec les mêmes couleurs.
Nous voyons là encore l’extrême similarité des résultats entre les deux matériaux. Les traces d’usure ont été observées à différents degrés d’usure (1 000, 5 000 et 10 000 cycles). Les images sont regroupées dans la figure 9 pour le nickel standard et dans la figure 10 pour le nickel sans acide borique.
Nous voyons que les traces d’usure sont très similaires pour les deux formulations de nickel, avec une taille de trace qui augmente proportionnellement au nombre de cycles. En outre, le transfert de matière de l’hémisphère vers le plan devient de plus en plus important, de même pour la formation de débris. Le volume d’usure, c’est-à-dire la quantité de matière perdue et transférée, ne cesse de croître en fonction du nombre de cycles. Ces résultats indiquent que le remplacement de l’acide borique n’a pas eu d’impact significatif sur les performances tribologiques des revêtements de nickel étudiés.
Les revêtements de nickel peuvent avoir différentes orientations cristallines en fonction de la formulation du bain, de la technique de dépôt utilisée et des conditions de dépôt. Les orientations cristallines courantes pour les revêtements de nickel incluent la texture de [111], [200] et [220]. La texture de [111] est souvent privilégiée pour les revêtements de nickel, car elle est généralement reliée à une bonne résistance à la corrosion et une dureté élevée. Les orientations cristallines des revêtements de nickel influent, en effet, sur leurs propriétés mécaniques et tribologiques, ainsi que leur résistance à la corrosion et leur adhérence aux substrats. C’est pourquoi une étude sur l’impact du remplacement de l’acide borique sur le nickel a été réalisée.
Les diagrammes de diffraction des rayons X obtenus sont illustrés dans la figure 11.
Les résultats de l’analyse de la structure cristalline des revêtements de nickel ont montré que les deux types de revêtements ont une structure cristalline très similaire avec une texture très proche, une taille de cristallites d’environ 15 nm dans les deux cas. Ces résultats indiquent que le remplacement de l’acide borique n’affecte pas significativement la structure cristalline du revêtement de nickel.
Nous avons également étudié l’impact du traitement thermique sur la structure cristalline des échantillons de nickel. Pour cela, les échantillons ont été placés dans une étuve à des températures de 125 °C et 300 °C pour une durée de 1 h 30. La figure 12 illustre les résultats obtenus pour le nickel standard et la figure 13, les résultats pour le nickel sans acide borique. À partir de ces graphiques, nous avons pu observer l’évolution de la taille des cristallites et de la texturation.
Les deux revêtements ont des cristallographies très similaires et des évolutions identiques après TT. Pour les deux revêtements, les deux premiers échantillons (la référence en bleu et l’échantillon à 125 °C en rouge) montrent des diffractogrammes similaires, tandis qu’une différence claire est observée pour l’échantillon à 300 °C en vert : les pics de diffraction sont plus fins, ce qui indique une augmentation de la taille des cristallites.
Deux tests ont été réalisés pour évaluer la résistance à la corrosion des deux revêtements de nickel. Le premier test, appelé NAV, correspond à une exposition des échantillons à des vapeurs d’acide nitrique (lié à la norme ISO 147674). Le second test est le test Clorox, pendant lequel les échantillons sont exposés à des vapeurs d’une solution d’eau de Javel à 3.5 % pendant 5 puis 15 minutes.
Ces tests permettent de simuler les conditions acides auxquelles les pièces peuvent être exposées dans certaines applications industrielles. Ils ont été réalisés sur des contacts 4PVH de connecteurs Airmax Vs© plaqués en laboratoire à 3 densités de courant différentes : 5, 10 et 20 ASD.
La figure 14 illustre les échantillons après le test NAV à 5 et 20 ASD pour le nickel standard et la figure 15 pour le nickel sans acide borique. Les résultats de ces deux tests sont une fois encore très peu discriminants, indiquant que le remplacement de l’acide borique ne semble pas avoir d’impact significatif sur la résistance à la corrosion du nickel.
III. Conclusion
Le tableau 1 présenté ci-dessous résume les différents tests effectués pour évaluer les performances des revêtements de nickel. Les critères évalués comprennent l’aspect visuel, les vitesses de placage dans des conditions de pH spécifiques, la morphologie, la dureté, le module de Young, la cristallographie et l’influence d’un traitement thermique, ainsi que la porosité et les tests de corrosion. Les résultats montrent qu’il’ n’y a pas d’impact significatif sur les performances du nickel lors du remplacement de l’acide borique par d’autres solutions tampons. Ces résultats sont très encourageants pour la poursuite des travaux sur le développement de revêtements de nickel alternatif. n

Figure A.
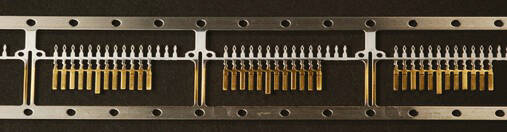
Figure B.
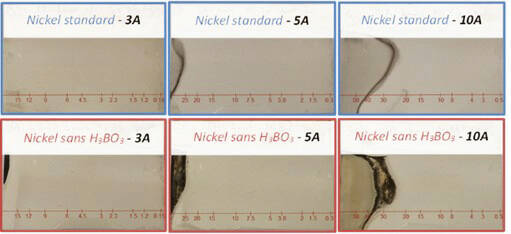
Figure 1 : Cellules de Hull des dépôts de nickel avec la formulation standard et avec la nouvelle formulation
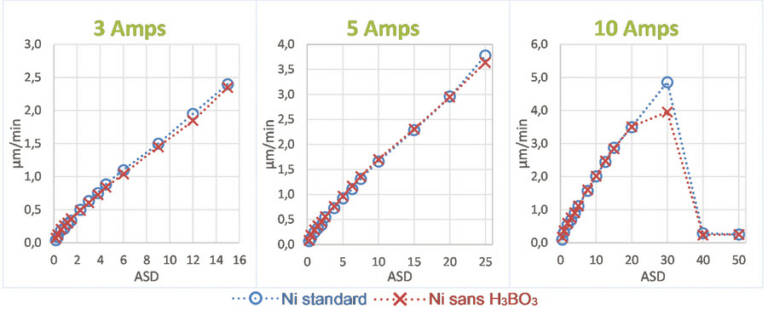
Figure 2 : Vitesses de placage en fonction de la densité de courant
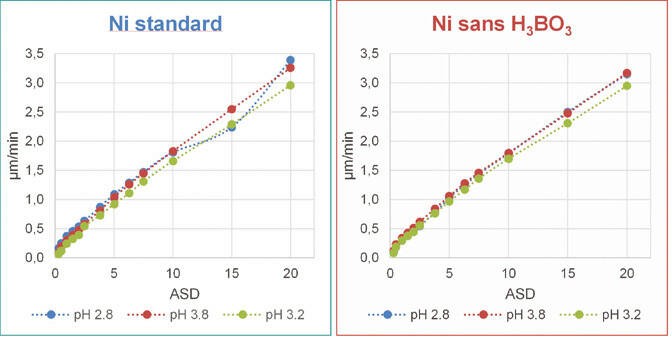
Figure 3 : Vitesses de placage en fonction de la densité de courant
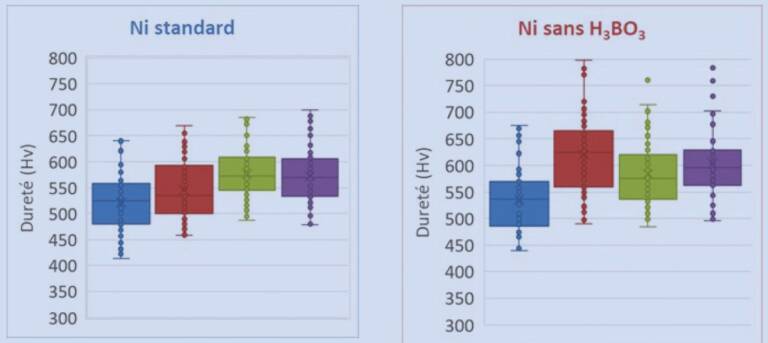
Figure 4 : Dureté du dépôt en fonction de la densité de courant pour les deux formulations, avec et sans acide borique.
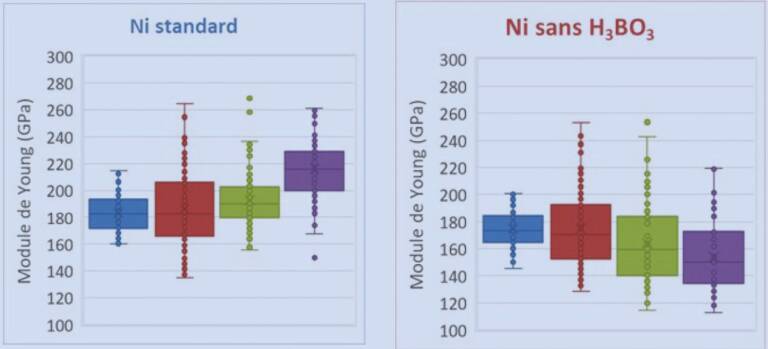
Figure 5 : Module de Young du dépôt en fonction de la densité de courant pour les deux formulations, avec et sans acide borique.
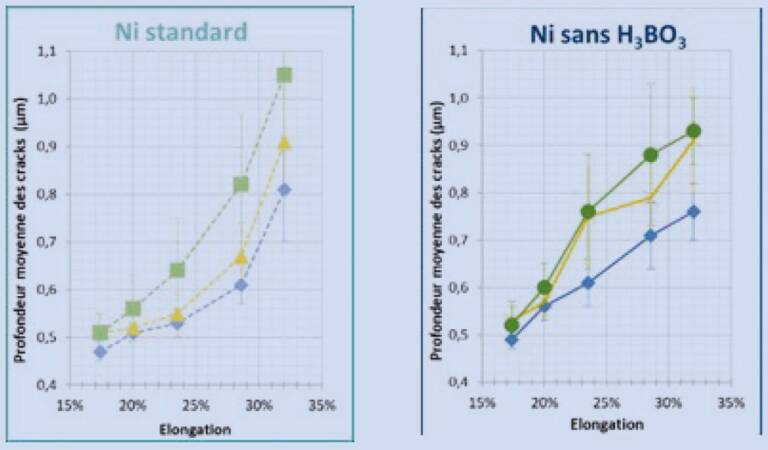
Figure 6 : Profondeur moyenne des cracks en moyenne, à 3 densités de courant, en fonction du pourcentage d’élongation pour les deux formulations étudiées.
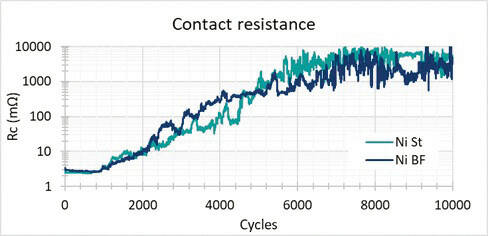
Figure 7 : Évolution de la résistance de contact en fonction des cycles de fretting
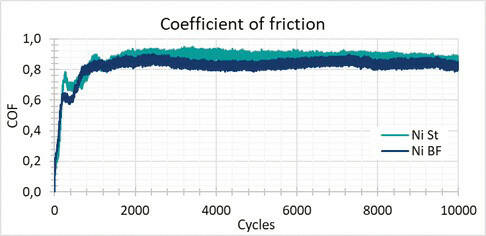
Figure 8 : Évolution du coefficient de frottement en fonction des cycles de fretting
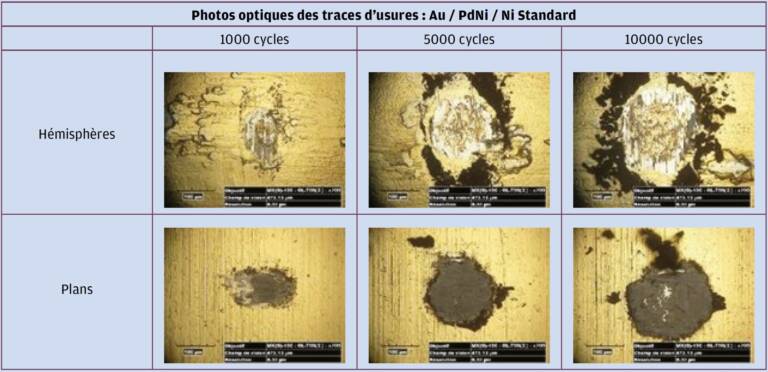
Figure 9 : Images optiques des hémisphères et des plans GXT© « standard » à différents nombres de cycles.
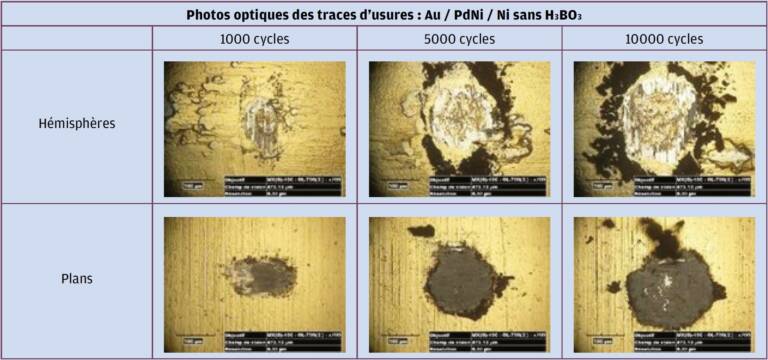
Figure 10 : Images optiques des hémisphères et des plans GXT© sans acide borique à différents nombres de cycles.
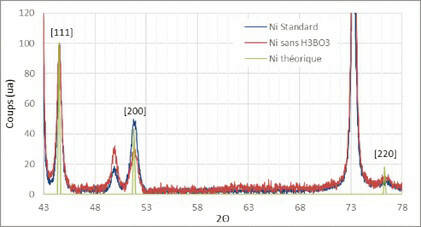
Figure 11 : Diagramme de diffraction des rayons X des revêtements de nickel avec et sans acide borique.
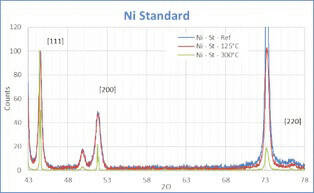
Figure 12 : Diagramme de diffraction des rayons X des revêtements de nickel standard, avant et après TT à 125°C et 300°C pendant 1h30
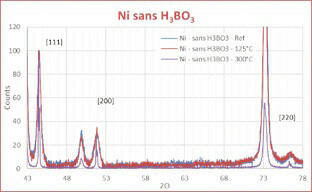
Figure 13 : Diagramme de diffraction des rayons X des revêtements de nickel sans acide borique, avant et après TT à 125°C et 300°C pendant 1h30
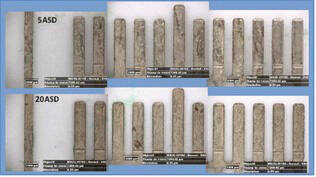
Figure 14 : Photos des échantillons après les tests NAV à 5 et 20ASD pour le nickel standard
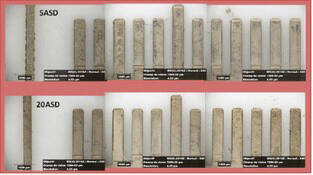
Figure 15 : Photos des échantillons après les tests NAV à 5 et 20ASD pour le nickel sans acide borique
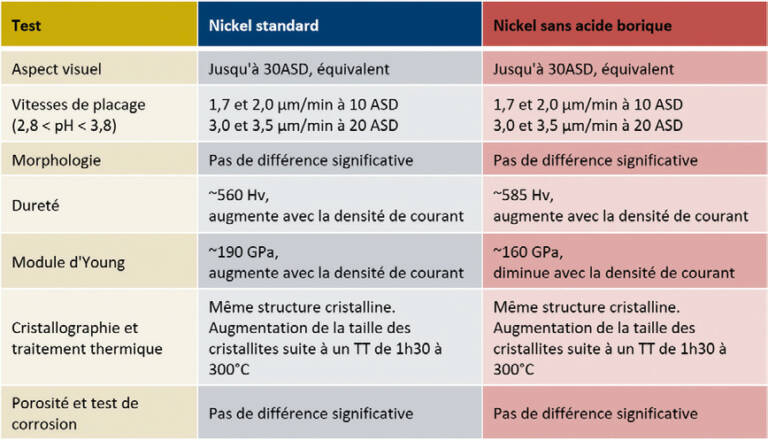
Tableau 1 : Les différents tests effectués pour évaluer les performances des revêtements de nickel.