Les traitements thermiques
Par Guy Murry, Ingénieur-conseil
Traitements d’homogénéisation, d’affinage, de restauration, de déshydrogénation, de détensionnement... autant de traitements thermiques qui ont pour objet d’améliorer et/ou de restaurer les potentialités des aciers.
Au cours de la mise en œuvre des aciers, il peut être nécessaire de les soumettre à des traitements thermiques particuliers qui ont pour objet d’améliorer et/ou de restaurer leurs potentialités. C’est ainsi que l’on peut :
• réduire les hétérogénéités chimiques dues au processus de solidification en réalisant un traitement d’homogénéisation,
• uniformiser la structure dans la masse et affiner les grains en effectuant un traitement d’affinage structural ou, dans certains cas, une normalisation,
• restaurer les propriétés mécaniques et physiques modifiées par un écrouissage en réalisant un traitement de restauration,
• éliminer l’hydrogène introduit dans le métal au cours d’un décapage acide ou d’un dépôt électrolytique en effectuant un traitement de déshydrogénation,
• relaxer les contraintes résiduelles générées au cours de la mise en œuvre du métal.
Le traitement d’homogénéisation
Selon l’Euronorm 52, ce traitement appelé parfois recuit d’homogénéisation ou de diffusion comporte un chauffage à une température généralement très supérieure à Ac3 suivi d’un maintien d’une durée suffisante pour que la diffusion atténue les hétérogénéités de composition chimique du métal. Il s’agit en effet de résorber plus ou moins les ségrégations apparues pendant la solidification en provoquant la diffusion des éléments d’alliage dont la teneur fluctue dans la masse du métal.
Pour approcher ce que doivent être les conditions opératoires, on peut utiliser la méthode proposée par Thelning1, méthode qui consiste à admettre que la teneur locale en l’élément ségrégé varie sinusoïdalement avec la distance. En appliquant les lois de la diffusion l’auteur est parvenu à l’équation suivante :
DCf = DCi exp( - D x t x p²/l²)
Avec :
DCf : écart maximal (en %) de teneur admis après le traitement,
DCi : écart maximal (en %) de teneur avant le traitement,
t : durée (s) du maintien à température,
l : distance (cm) entre un point où la teneur est maximale et le point le plus voisin où elle est minimale,
D : coefficient de diffusion (cm²/s) de l’élément d’alliage considéré à la température du traitement sachant que :
D = Do exp(- Q/RT)
Avec :
Do (cm²/s) : facteur de fréquence,
Q (J.mol-1) : énergie d’activation de la diffusion,
T (K) : température absolue de traitement,
R = 8,314 J.mol-1.K-1
Données à titre d’exemples d’application de cette méthode :
• La figure 1 permet d’apprécier la forte influence de la température sur l’efficacité F du traitement, laquelle est ici estimée à travers la réduction relative du gradient de teneur en l’élément considéré (ici le manganèse dans un acier non allié) soit :
F = 100 x (DCi - DCf) / DCi
=
100 x (1 - exp (- D x t x p² / l²)
• La figure 2 permet d’apprécier la forte influence de la durée du maintien à la température de 1 100 °C sur l’efficacité F du traitement, laquelle est encore ici estimée à travers la réduction relative du gradient de teneur en l’élément considéré (ici le manganèse ou le nickel ou le vanadium).
Ces schémas donnent un complément de sens aux deux termes de la définition rappelée plus haut :
• « Une température généralement très supérieure à Ac3 » et, en fait, au moins du niveau de 1 100 °C.
• « Un maintien d’une durée suffisante » qui peut être de l’ordre de plusieurs centaines d’heures.
Ces éléments montrent que, industriellement, l’homogénéisation ne pourra pas être complète et d’autre part ils donnent à penser que les conditions opératoires provoqueront un fort grossissement des grains, il sera donc nécessaire d’affiner ultérieurement ces derniers en réalisant un traitement d’affinage structural.
Le traitement d’affinage structural et la normalisation
Le traitement d’affinage structural
Selon l’Euronorm 52, ce traitement appelé parfois recuit d’affinage structural ou recuit de régénération comporte un chauffage à une température légèrement inférieure à Ac3 suivi d’un maintien de courte durée et d’un refroidissement à vitesse convenable en vue d’affiner ou de régulariser le grain de l’acier dans toute la masse après que celui-ci ait subi un grossissement excessif à la suite, par exemple, d’une surchauffe accidentelle ou d’un traitement d’homogénéisation.
L’affinement des grains de l’acier est possible grâce à la transformation a´g et au processus de germination et de croissance des constituants. Il se produit donc :
• Pendant le chauffage, quand la température de l’acier est comprise entre les points de transformation (voir les diagrammes de transformation en chauffage continu). De ce fait, la température maximale atteinte au cours de ce traitement d’affinage est généralement limitée à un niveau :
• Supérieur à Ac3 mais très voisin de ce dernier pour les aciers hypoeutectoïdes.
• Supérieur à Ac1 mais très voisin de ce dernier pour les aciers hypereutectoïdes. Il n’est pas nécessaire de mettre tous les carbures en solution.
Tout chauffage à une température supérieure à ces limites provoquerait un nouveau grossissement des grains d’austénite, qui réduirait d’autant l’efficacité du traitement.
• Pendant le refroidissement si celui-ci est réalisé dans des conditions telles qu’après retour à la température ambiante, la structure de l’acier soit constituée de ferrite (ou de cémentite) et de perlite fines. Pour que les grains de ferrite et de perlite soient les plus petits possible, il faut que le refroidissement soit le plus rapide possible mais que, bien entendu, il ne provoque pas la formation de bainite. La loi de refroidissement doit donc être plus lente que la loi critique de transformation bainitique (repérée LB DtB sur la figure 3) mais néanmoins proche. En effet, dans le domaine de formation de ces structures, la grosseur des grains de ferrite et de perlite diminue quand la vitesse de refroidissement augmente, ces constituants se formant alors à des températures de plus en plus basses.
La durée du maintien à la température maximale du cycle doit seulement permettre d’assurer la mise en température uniforme de la pièce : sa durée sera donc réduite au minimum nécessaire pour obtenir ce résultat. Tout allongement inutile de cette durée ne pourrait qu’engendrer un début de grossissement des grains d’austénite.
La normalisation
Selon l’Euronorm 52, cette expression est utilisée couramment pour désigner un traitement comportant une austénitisation suivi d’un refroidissement à l’air calme. Mais il faut noter que cette norme précise que « dans le cas des aciers non alliés ou faiblement alliés ce traitement est destiné à produire une structure aussi voisine que possible de la perlite fine ». Cette définition est équivalente à celle du traitement d’affinage structural. Elle substitue simplement le refroidissement à l’air à un refroidissement optimisé en limitant le domaine d’utilisation aux aciers non alliés ou faiblement alliés c’est-à-dire aux aciers à faible trempabilité. Mais alors, il est prudent de tenir compte du fait que, comme le précise la norme, « par suite de l’influence des dimensions et de la forme de la pièce sur la loi de refroidissement, l’état final peut, pour une même nuance d’acier, varier plus ou moins ».
Le traitement de restauration
Ce traitement consiste à porter un acier écroui (c’est-à-dire un acier qui a subi une déformation plastique) à une température inférieure à Ac1 afin de rétablir, au moins partiellement, ses propriétés mécaniques et physiques modifiées par l’écrouissage mais sans changer sa structure. Il diffère en cela du traitement de recristallisation qui modifie très sensiblement la structure en provoquant, dans le métal écroui, la germination et la croissance de nouveaux grains.
La restauration des propriétés mécaniques de l’acier écroui se traduit par l’abaissement des caractéristiques de résistance et l’augmentation des caractéristiques de ductilité. Ces évolutions sont dues alors à la diminution du nombre des défauts ponctuels et à la diminution de la densité des dislocations qui, par ailleurs, se réarrangent par glissement et montée.
Le paramètre important du traitement de restauration est la température à laquelle est porté le métal. Elle est relativement modérée et, en général, comprise entre 150°C et 500°C (la restauration étant toutefois d’autant plus importante que la température atteinte est plus élevée). Elle doit rester, bien entendu, toujours inférieure à la température de recristallisation et de ce fait la restauration n’est jamais complète. Aux plus basses températures auxquelles cette dernière peut être entreprise (entre 100 et 200°C environ), elle provoque une remontée de la limite d’élasticité due au commencement de la relaxation des contraintes résiduelles du métal, relaxation qui diminue l’instabilité mécanique de la structure.
La durée du maintien en température a une influence plus faible que celle du niveau de la température car, si elle est sensible au début du maintien (disons pratiquement dans la première heure) elle devient ensuite du second ordre de telle sorte que l’effet de la restauration tend globalement, pour chaque température, vers un niveau quasi asymptotique lui-même dépendant de cette dernière. Un exemple de ces évolutions est donné par le graphique représenté à la figure
Le traitement de déshydrogénation
A la suite d’un décapage dans un acide non oxydant ou après une opération de revêtement métallique par électrolyse, l’acier peut être chargé en hydrogène. Cet hydrogène occlus engendre une fragilisation susceptible de provoquer une rupture plus ou moins différée sous une contrainte bien inférieure à la charge de rupture. Ce phénomène est particulièrement sensible avec les aciers dont la dureté est élevée, mais il peut encore éventuellement se manifester dans des aciers dont la dureté est voisine de 400 HB. Il est donc indispensable d’éliminer cet hydrogène.
On constate que, s’il n’est pas retenu par un revêtement métallique (de Cr, Zn, Cd. Ni, Sn, Pb ou Ag), l’hydrogène peut se dégager au cours d’un séjour à la température ambiante mais ce processus est lent. Aussi procède-t-on à un traitement de déshydrogénation qui a pour but de provoquer le dégagement de l’hydrogène occlus dans un acier sans modifier sa structure.
La pratique courante consiste à porter l’acier à une température de l’ordre de 150 à 200 °C et à le maintenir à cette température pendant une durée assez longue (de l’ordre de 5 à 15 h). Cette durée de maintien peut être diminuée si l’on porte la température à environ 300 °C, mais il est alors nécessaire de prendre des mesures pour éviter l’oxydation de la surface du métal.
Si l’hydrogène est susceptible d’être retenu par un revêtement métallique (de Cr, Zn, Cd. Ni, Sn, Pb ou Ag), on interrompt une ou plusieurs fois le dépôt avant qu’il ait atteint son épaisseur finale et on procède à chaque arrêt à un traitement de déhydrogénation.
Le traitement thermique de détensionnement
Dit aussi « traitement de relaxation » (ne pas confondre avec « traitement de détente » = revenu de la martensite vers 180-200 °C), ce traitement a pour objet de diminuer ou d’éliminer les contraintes résiduelles (générées au cours de la mise en œuvre du métal par usinage, formage à froid, soudage, trempe et plus généralement lors de toute déformation plastique localisée).
Ces contraintes résiduelles peuvent être à l’origine de déformations irréversibles apparaissant lors d’un usinage de finition mais, surtout, elles peuvent affecter le comportement en service de la construction. Elles s’ajoutent en effet algébriquement aux contraintes de service et il est alors nécessaire de distinguer deux situations :
• Si les contraintes résiduelles sont de traction : elles augmentent les sollicitations de traction et peuvent alors être responsables :
• d’une surcharge locale du métal conduisant à une déformation plastique, voire à une rupture,
• d’une baisse de la tenue à la fatigue de la construction (raccourcissement de la durée de vie),
• d’un risque de rupture fragile,
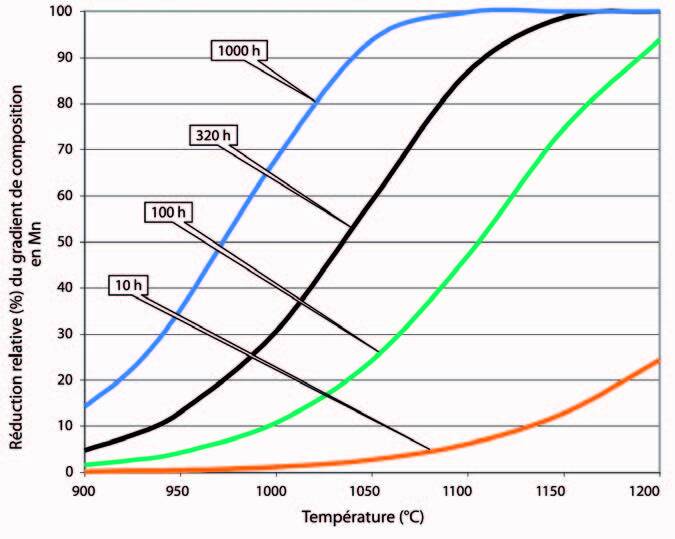
Figure 1 : Influence de la température sur l’efficacité de traitements avecdifférentes durées de maintien.
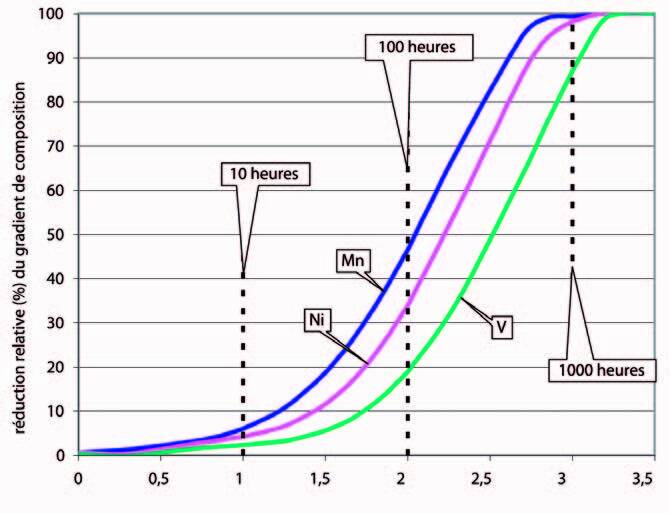
Figure 2 : Influence de la durée du maintien en température sur l’efficacité d’un traitementd’homogénéisation
à 1 100°C.
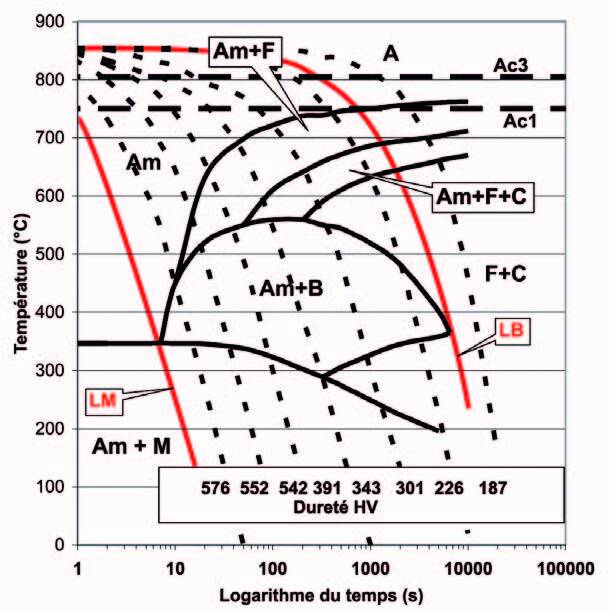
Figure 3 : Diagramme TRC d’un acier 35CrMo4. A = austénite. Am = austénite métastable. F = ferrite. C = carbure.
B = bainite. M = martensite.
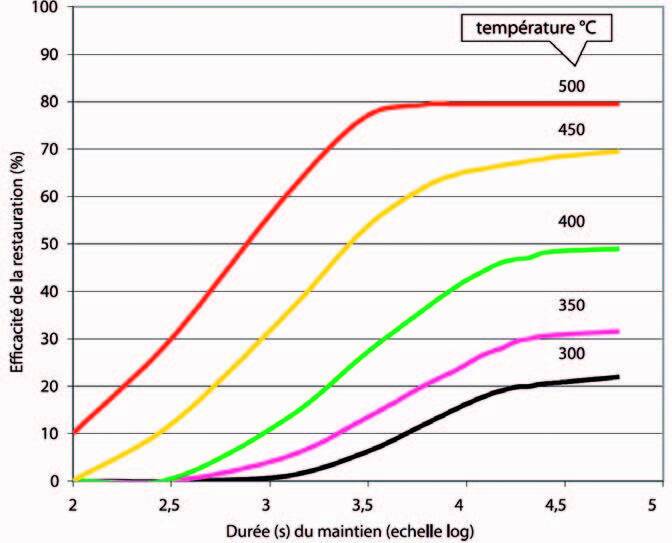
Figure 4 : Efficacité de la restauration (en %) d’un acier non allié en fonction de la température et de la durée
du maintien (d’après les résultats de LESLIE).
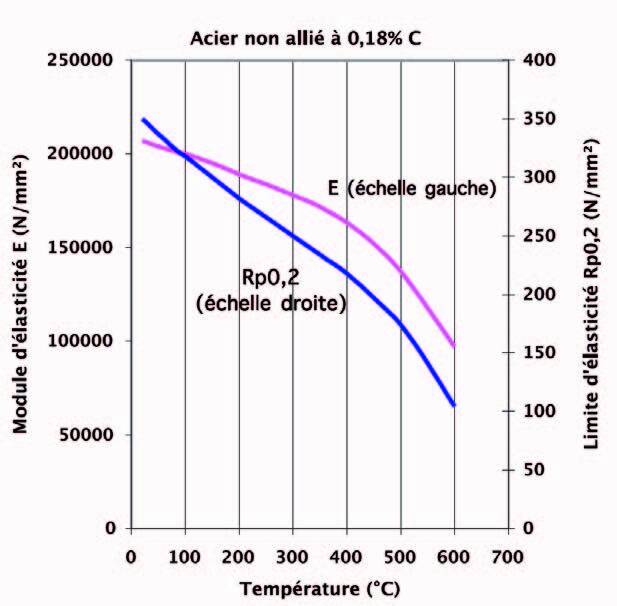
Figure 5 : Variation avec la température de la limite d’élasticité d’un acier non allié à 0,18 %C.
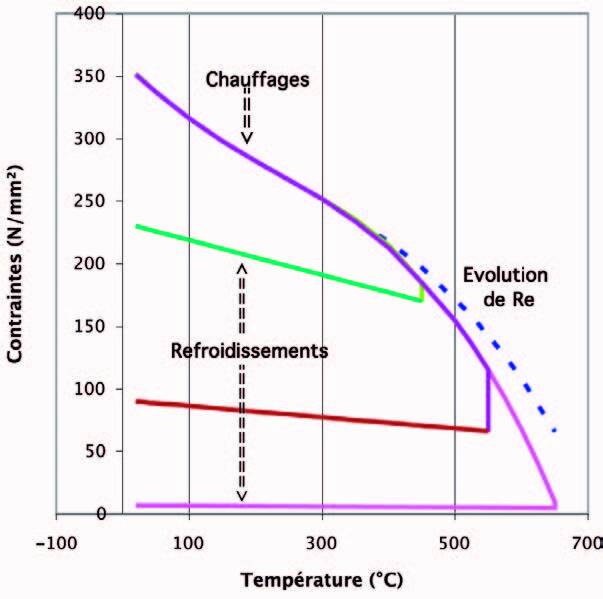
Figure 6 : Résultats d’essais de relaxations différentiels anisothermes sur un acier non allié à 0,18 %C.
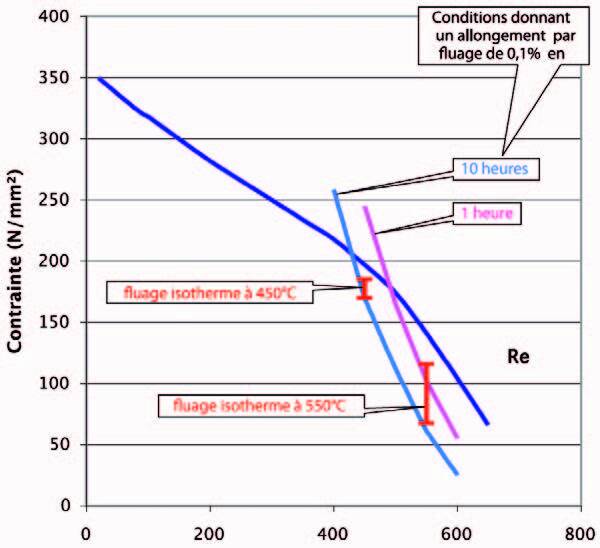
Figure 7: Données relatives à la réalisation d’une déformation par fluage de 0,1% (ordre de grandeur de la déformation élastique correspondant ici à Re) en 1 heure ou en 10 heure.
• par ailleurs, sur des alliages particuliers et en présence d’un environnement spécifique, elles peuvent initier une corrosion sous tension.
• Si les contraintes résiduelles sont de compression : elles diminuent alors les sollicitations de traction et améliorent globalement le comportement mécanique de la construction (notamment en fatigue).
Il est donc opportun d’intervenir pour, au moins, abaisser le niveau des contraintes résiduelles de traction et éventuellement, éliminer toutes les contraintes résiduelles de traction.
Mécanisme de la relaxation des contraintes résiduelles
Pour comprendre le mécanisme de la relaxation des contraintes résiduelles, il suffit de remarquer que ces contraintes résiduelles existent parce que le métal est soumis à une déformation élastique. On sait que l’on a la relation de base :
Dle / lo = s / E.
Elle définit le comportement élastique d’un matériau à travers sa déformation élastique Dle rapportée à la longueur initiale lo et à partir de la contrainte appliquée s et du module d’élasticité E.
Si l’on écrit cette relation sous la forme s = E x Dle / lo, on voit que pour diminuer s il faut diminuer Dle. Or cette déformation, due à des phénomènes qui se sont produits antérieurement, est permanente. Il ne reste donc qu’une possibilité : transformer au moins partiellement la déformation élastique en déformation plastique Dlp. En effet, si l’on a Dle qui devient Dl’e + Dlp avec toujours Dl’e + Dlp = Dle, la contrainte résiduelle ne sera plus que s‘ = E x Dl’e / lo inférieure à s (puisque Dl’e est plus petit que Dle).
Détensionnement par traitement thermique
Au cours de ce traitement on fait en sorte que les contraintes résiduelles provoquent elles-mêmes la plastification nécessaire à leur relaxation. Pour ce faire, on ne peut jouer que sur les performances mécaniques du métal et essentiellement :
• Sur un abaissement réversible de sa limite d’élasticité de telle sorte que, sous l’action de ses propres contraintes résiduelles, le métal subisse une déformation plastique. Cette diminution est obtenue par une élévation de la température du métal qui va aussi provoquer une diminution réversible du module d’élasticité. La figure 5 donne un exemple de ces évolutions pour un acier non allié. Généralement la limite d’élasticité chute en deux temps : une chute lente aux températures peu supérieures à la température ambiante et une chute plus rapide aux températures plus élevées. La baisse du module d’élasticité est plus régulière.
• Sur un mode particulier de déformation plastique, le fluage qui intervient ici si la température est correctement ajustée. Le fluage est un processus de déformation plastique (se produisant à température supérieure à la température ambiante) qui a pour particularité principale de pouvoir se développer dans le temps, éventuellement jusqu’à rupture, alors qu’à la fois la température et l’effort appliqué (inférieur à la résistance à la traction à la température considérée) restent constants.
Pour analyser ces différents comportements on recourt à des essais de relaxation anisothermes et différentiels (différentiels car pendant les variations de température on compense la dilatation de l’éprouvette pour ne considérer que sa déformation mécanique). De tels essais donnent des résultats du type de ceux présentés sur la figure 6. Il s’agit de courbes décrivant les évolutions de la contrainte résiduelle (fixée, au départ, au niveau de la limite d’élasticité à 20 °C) d’un acier non allié à 0,18 % C en fonction de la température et du temps au cours de cycles thermiques comprenant un chauffage lent (ici 80°C/h), un maintien à la température maximale (ici 4 heures) et un refroidissement lent (ici 80 °C/h).
A l’examen de telles courbes on constate :
• qu’au cours du chauffage, au-delà de 350°C environ, le niveau de la contrainte décroît plus que ne le fait celui de la limite d’élasticité,
• qu’au cours d’un maintien à la température maximale de chaque cycle la contrainte résiduelle diminue.
Ces comportements s’expliquent par l’intervention du fluage. En effet, il est très probant de superposer sur le graphique décrivant les variations de la limite d’élasticité à chaud les courbes définissant les conditions dans lesquelles le fluage peut intervenir ici, à savoir les données relatives à la réalisation d’une déformation par fluage de 0,1% (ordre de grandeur de la déformation élastique correspondant ici à Re) en 1 heure ou en 10 heures (figure 7). On constate ainsi l’importance du fluage dans le processus de relaxation des contraintes résiduelles, fluage qui intervient déjà pendant le chauffage dès 450°C environ et qui se poursuit pendant le maintien isotherme (la figure rappelle ce qu’a été le fluage isotherme lors dès essais décrits par la figure 6). A ce sujet, il est important de noter que la relaxation isotherme qui se développe au cours des maintiens est sensible pendant quelques heures mais qu’ensuite la baisse de la contrainte qui subsiste ne permet plus la poursuite du fluage à la température considérée. Par ailleurs, l’ampleur du fluage isotherme varie avec le niveau de température. Elle est faible aux « basses » températures (le métal est trop résistant) ainsi qu’aux « hautes » températures (le fluage s’est déjà développé pendant le chauffage) et maximale aux températures intermédiaires.
Les modalités du détensionnement
Le traitement de détensionnement comprend un chauffage, un maintien en température pendant lequel le fluage se développe et un refroidissement.
• Conditions de chauffage
Ce chauffage d’un métal partiellement sous contrainte doit être réalisé assez lentement pour éviter que des écarts de température trop importants ne génèrent de nouvelles déformations et donc des contraintes supplémentaires. Il sera d’autant plus lent que le métal aura une conductivité thermique faible et que la pièce sera plus massive. Il devra atteindre la température optimale qui sera choisie en fonction de l’alliage traité de telle sorte que :
• elle soit assez élevée pour que, non seulement, la limite d’élasticité soit assez basse mais aussi pour que le fluage puisse intervenir,
• elle ne soit pas trop élevée au point que les propriétés du métal soient affectées par des évolutions structurales dues à un effet de revenu supplémentaire (avec coalescence des précipités et donc perte des performances mécaniques).
Pratiquement on choisit souvent la température la plus élevée qui n’affecte pas encore la structure et donc les propriétés du métal.
• Durée de maintien à la température choisie
Pratiquement on peut dire qu’au delà d’un maintien de 5 à 10 heures l’évolution des contraintes résiduelles devient négligeable et qu’il n’est donc pas économique de poursuivre le maintien.
Cette durée ne prend pas en compte, bien entendu, le temps nécessaire pour que toute la pièce soit pratiquement portée en tous points à la même température.
• Le refroidissement
Il sera lent pour éviter de créer des écarts de température trop importants qui provoqueraient l’apparition de nouvelles contraintes et d’autant plus lent que le métal aura une conductivité thermique faible et que la pièce sera plus massive.
Il sera toutefois nécessaire de tenir compte du risque de manifestation de phénomènes perturbateurs susceptibles de se produire pendant un refroidissement trop lent telle que la fragilité réversible de revenu, par exemple.
Autres conséquences d’un tel traitement
Le cycle thermique d’un traitement de détensionnement est tout à fait comparable à un cycle de revenu et il peut donc en avoir les mêmes conséquences. Le risque de sur-revenu a été mentionné mais on peut noter aussi le risque de restaurer les propriétés mécaniques d’un métal écroui et donc de perdre une partie au moins du durcissement par écrouissage. Mais il peut être intéressant de profiter de la possibilité de conjuguer traitement de détensionnement et revenu de durcissement par précipitation.