Simulation de la trempe de pièces de mécanismes de sièges automobiles avec le logiciel qobeo® : un grand pas en avant dans la compréhension et la maîtrise du processus
Par David EVEN, Mariana MAYER GRIGOLETO, FORVIA Faurecia Seatin
Faurecia participe depuis 2015 au développement du logiciel qobeo®, qui permet de prendre en compte les installations de traitement thermique dans leur ensemble ainsi qu’un chargement de plusieurs pièces, en considérant la mécanique des fluides, le transfert de chaleur (y compris le rayonnement émis et reçu) et un nouveau modèle d’ébullition. Initialement, la simulation se concentrait sur une seule pièce.
Le site FORVIA Faurecia Seating de Caligny est spécialisé dans la conception et la fabrication de mécanismes de sièges automobiles (Figure 1). Ces produits nécessitent une grande précision dimensionnelle ainsi que des propriétés mécaniques élevées pour répondre aux exigences de qualité perçue en service, de fatigue, de durabilité et de résistance au crash.
Les traitements thermiques utilisés jusqu’à présent sont principalement la trempe et la carbonitruration, et ce depuis des décennies. Afin d’anticiper encore mieux les déformations après traitement thermique, les transformations métallurgiques ainsi que l’impact de la dispersion des paramètres matériau et procédé sur un lot de pièces, Faurecia investit depuis dix ans dans la simulation numérique de ces procédés.
Initialement, la simulation se concentrait sur une seule pièce, en supposant que les conditions environnantes étaient connues et parfaites, telles que la température dans le four, le potentiel de carbone ou encore l’échange de chaleur dans le bac de trempe. Cela correspond à l’état de l’art actuel dans le monde industriel.
Pour aller plus loin dans la représentativité des modèles, Faurecia participe depuis 2015 au développement du logiciel qobeo®, qui permet de prendre en compte les installations de traitement thermique dans leur ensemble ainsi qu’un chargement de plusieurs pièces, en considérant la mécanique des fluides, le transfert de chaleur (y compris le rayonnement émis et reçu) et un nouveau modèle d’ébullition.
Ce dernier calcule l’échange thermique local entre une pièce et le milieu de trempe, en fonction de sa géométrie, de sa position et de son orientation dans le bac de trempe, donnant accès à une visualisation inédite et parfois inattendue – mais néanmoins réaliste – du refroidissement.
Cet article vise à donner un aperçu de ce que les derniers développements en matière de simulation numérique peuvent apporter à la compréhension du processus de trempe.
Approche classique de la simulation de la trempe
Les usines de Faurecia Seating sont équipées de lignes de carbonitruration, comme le montre la Figure 2. À la sortie du four, les pièces tombent par gravité dans le bac de trempe contenant de l’huile à 60 °C. La trajectoire précise ; l’orientation et le temps de chute ne sont pas connus, car l’huile est opaque et les parois du bac ne disposent pas de fenêtre.
L’écoulement de l’huile a toutefois été étudié en simulation CFD (Computational Fluid Dynamic), comme le montre la Figure 3. Toutefois, pour simuler le refroidissement des pièces, l’ensemble des coefficients d’échange thermique (HTC), en fonction de la température de surface des pièces, doit être connu à l’avance[1]. Pour ce faire, le test de drasticité (ISO9950[2]) a été simulé pour obtenir par rétro-ingénierie cet ensemble de coefficients[3]. Cependant, cet ensemble de HTC n’est valable que pour un fluide, une vitesse d’agitation de ce fluide et une géométrie donnée de la pièce. Il implique que le flux de chaleur entre la surface de la pièce et le fluide est le même tout autour de la pièce pour une température donnée, sauf si l’on s’efforce d’identifier les HTC sur plusieurs géométries[4].
Nouvelle approche de modélisation pour la simulation de la trempe, prenant en compte l’ébullition du fluide
Cette limitation a motivé le lancement de la chaire industrielle Infinity, cofinancée par l’ANR et un consortium de douze entreprises françaises – dont Faurecia Seating – et dirigée par le Pr. Elie Hachem au Cemef, à Sophia-Antipolis. Les travaux de recherche [5],[6],[7],[8],[9] se sont déroulés sur une période de cinq ans (2018-2023) et le résultat est une mise à jour majeure du logiciel qobeo®, commercialisé et maintenu par Sciences Computers Consultants (SCC). Dans cette nouvelle version, un film de vapeur est initialisé autour de la pièce. Le code de simulation combine le transfert de chaleur, la CFD et une procédure spécifique (Figure 4) pour calculer l’évolution du film de vapeur en fonction du temps et de la température. En conséquence, le flux de chaleur entre la pièce et le fluide est calculé localement à chaque instant. L’algorithme prend en compte les effets de mouillage ainsi que le flux de chaleur critique pour maintenir ou non l’ébullition du fluide. Si la température de la pièce est devenue trop basse pour maintenir le mode d’ébullition activé, la convection classique avec contact direct entre le fluide et la surface de la pièce est alors utilisée pour le calcul thermique. En conséquence, les trois étapes bien connues de caléfaction, d’ébullition nucléée et de convection (Figure 5) peuvent être modélisées. Afin de rendre le temps de calcul compatible avec les besoins industriels, la simulation de l’ébullition est effectuée sur une courte période, jusqu’à ce que le film de vapeur soit stabilisé pour calculer le flux de chaleur maximal. Cette information est ensuite transférée à la pièce pour calculer la température à l’intérieur (Figure 4). Des modèles métallurgiques ont également été implémentés afin de calculer les proportions finales de phases métallurgiques.
Validation de la nouvelle approche de modélisation sur l’essai de drasticité
L’essai de drasticité[2] est un essai relativement simple et largement utilisé dans l’industrie pour contrôler la qualité et les performances de l’huile de trempe : une canne est équipée d’un thermocouple au centre géométrique d’un cylindre en Inconel 600 de 12,5 mm de diamètre et de 66mm de longueur. Ce cylindre est chauffé à 850 °C puis plongé rapidement dans deux litres d’huile de trempe portée à 40 °C. La température en fonction du temps est enregistrée pendant une minute, ce qui est suffisant pour refroidir le cylindre d’Inconel du mode d’ébullition au mode de convection. De plus, un verre transparent peut être utilisé pour contenir l’huile : il est alors possible d’observer l’ébullition et la convection à la surface de la pièce, ce qui rend la comparaison avec la simulation très intéressante.
Les figures 6 et 7 comparent les résultats entre la simulation et l’essai expérimental. La forme du film de vapeur est correctement prédite. Le point chaud du cylindre en Inconel est légèrement différent dans la simulation et dans l’expérience, probablement en raison des limitations actuelles de définition des conditions aux limites dans le tube avec la version bêta de qobeo® utilisée dans ces travaux. La figure 7 met en évidence la valeur ajoutée du modèle d’ébullition : sans ébullition, la courbe obtenue avec la simulation surestime considérablement la température. Seule la physique, en effet, de la convection est prise en compte. Avec le modèle d’ébullition, la phase d’ébullition est bien prédite de 0 à 10 secondes. Le mode de refroidissement passe ensuite de l’ébullition à la convection, avec une bonne corrélation entre l’expérience et la simulation. Le flux de chaleur de caléfaction reste sous-estimé dans les toutes premières secondes, ce qui montre qu’il existe encore une amélioration possible.
Application industrielle sur une pièce simple
Afin d’étudier l’effet de l’orientation de la pièce dans le bac de trempe et de sa géométrie sur l’efficacité de la trempe, une pièce simple a été conçue en tenant compte de la géométrie des pièces de mécanisme, telle que la semi-découpe, typique du procédé de découpage fin, comme le montre la figure 8. En raison de la complexité de la mise en œuvre de thermocouples dans le processus réel par l’expérience, seules des simulations numériques ont été réalisées.
La figure 9 montre les résultats pour cinq orientations de la pièce et apporte une meilleure compréhension de la dispersion inhérente au processus de trempe : avec l’approche classique utilisant les HTC, les dix courbes seraient superposées. Avec le modèle d’ébullition, on observe des effets locaux tels que le piégeage de la vapeur, les effets de bord et même les effets de « ventouse ». L’orientation à 0° met en évidence l’effet de piégeage de la vapeur avec un film épais à l’intérieur de la semi-découpe. De manière surprenante, mais logique, l’orientation à 180° met en évidence l’effet de ventouse sur les surfaces supérieures horizontales : le film de vapeur s’épaissit en raison de la difficulté qu’il a à se décoller de la surface de la pièce. L’orientation à 90° met en évidence l’accumulation de vapeur sur l’extrémité supérieure de la pièce. Chaque cas met en évidence un gradient de température élevé à l’intérieur de la pièce qui, une fois de plus, n’a pas pu être pris en compte avec les HTC définis à priori. L’orientation à 180° est, du point de vue du gradient de température, la meilleure pour minimiser les contraintes internes et obtenir la dureté la plus homogène après la trempe. Même si les cinq orientations peuvent donner les mêmes résultats métallurgiques pour une nuance d’acier présentant une bonne trempabilité, on peut s’attendre à ce que la distorsion soit différente en raison des gradients thermiques.
Application industrielle sur une pièce de mécanisme de géométrie complexe
Pour aller plus loin et se rapprocher des besoins industriels, le flasque mobile d’une articulation de dossier de siège (figure 10) a été modélisé. On s’intéresse en particulier aux zones de butée aux extrémités, car elles sont potentiellement candidates au phénomène de piégeage de vapeur. Deux orientations sont étudiées (cas A et B) ainsi qu’un cas présentant une pièce au-dessus d’une autre (cas multi-charges), comme le montre la figure 11. Deux capteurs sont placés dans la zone d’intérêt des butées.
Pour la première fois, il est possible de visualiser les interactions du flux d’huile et du film de vapeur sur le refroidissement des pièces, comme le montre la figure 12. Dans le cas « multi-charges », le flux de vapeur est accéléré grâce à l’aspiration de la pièce supérieure. Les deux pièces interagissent, en effet, l’une avec l’autre : la pièce supérieure « aspire » la vapeur de la pièce inférieure, tandis que la vapeur de la pièce inférieure s’accumule sous la pièce supérieure. Selon l’orientation des pièces (cas A vs cas B), les butées ne souffrent pas de la même accumulation de vapeur et les courbes de refroidissement sont donc très différentes (figure 13, à gauche) : le cas B présente un refroidissement plus lent que le cas A, car le cas B présente une orientation plus proche de l’horizontale que le cas A. Dans le cas multi-charges, la pièce supérieure présente un refroidissement plus lent mais plus homogène, en raison de l’accumulation de vapeur provenant de la pièce inférieure sur les butées. L’ensemble des courbes de refroidissement montre une dispersion significative qui est probablement plus proche de la réalité que la courbe unique prédite par l’approche HTC classique (figure 13, à droite). Dans l’approche classique, les HTC ont été identifiés sur la base d’un test de drasticité. Ce test, à l’emplacement du thermocouple (à mi-longueur du cylindre d’Inconel), ne souffre pas d’accumulation de vapeur (figure 6). Cela peut expliquer pourquoi le refroidissement simulé est plus rapide dans le mode d’ébullition avec l’utilisation des HTC que dans la simulation avec le modèle d’ébullition.
La figure 14 met en évidence l’hétérogénéité de la température en surface, pour un temps donné correspondant à la phase d’ébullition nucléée et pour les trois cas étudiés. Malgré la quasi axi-symétrie de la pièce, le contour de température est loin d’être homogène par rapport à l’axe de révolution, ce qui est un résultat très différent de l’approche classique HTC.
Les calculs métallurgiques sur le cas A donnent des résultats intéressants (figure 15) : lorsque la vapeur s’accumule, la vitesse de refroidissement est plus lente et – résultat logique – la transformation de l’austénite en martensite se termine dans cette zone. Même si la pièce est entièrement martensitique après la trempe, cet effet peut expliquer la déformation hétérogène de la pièce.
Conclusion
La chaire industrielle Infinity a permis de développer un modèle d’ébullition capable de simuler avec une très bonne précision le processus de trempe, en prenant en compte le film de vapeur local et en calculant ainsi le flux de chaleur échangé entre la pièce et le fluide de trempe. Il s’agit d’une approche révolutionnaire dans le domaine de la simulation du traitement thermique qui permet d’étudier de nombreux problèmes rencontrés dans la production industrielle de composants automobiles. Ce qui n’était auparavant qu’une hypothèse d’expert en traitement thermique pour expliquer certains problèmes peut désormais être visualisé et confirmé par un outil scientifique.
Grâce au travail de recherche effectué sur la réduction du temps de calcul, les simulations présentées dans ce document ont été effectuées en moins d’une journée avec 16 cœurs, ce qui est tout à fait acceptable pour des cas aussi complexes.
Ce logiciel ouvre de nouvelles portes dans la validation du processus de traitement thermique, permettant de réduire les temps de développement et de gagner en confiance en termes de qualité et de capacité du processus pour les pièces soumises à des contraintes de sécurité et de réglementation.
Les prochains défis à relever pour être pleinement représentatif du processus réel sont les suivants :
la modélisation d’un lot complet de pièces (20 à 50) tombant simultanément dans le bac de trempe ;
une meilleure modélisation de l’interaction entre l’agitation de l’huile provenant de la turbine du réservoir et le flux de vapeur à la surface de la pièce ;
un modèle mécanique abouti permettant d’aller jusqu’au calcul de la géométrie finale de la pièce.
Remerciements
Pour avoir rendu ce travail possible, les auteurs tiennent à remercier :
L’Agence nationale de la recherche (ANR) ;
Giulia Lissoni et Lucas Sardo de Sciences Computers Consultants (SCC) ;
Elisabeth Massoni, Elie Hachem, Rudy Valette, Charles Brissot, Sacha El Aouad, Ghaniyya Medghoul, Joe Khalil et Ali-Malek Boubaya du Cemef ;
Gérard Perreau et Odile Alleaume de Fuchs ;
Mathieu Saboureau, Aurélie Achille et Bruno Duchesne de Faurecia ;
ainsi que les représentants des entreprises suivantes pour leur participation à la chaire industrielle Infinity : ArcelorMittal, Aubert & Duval, Cefival, CMI, Framatome, Lisi Aerospace, Linamar Montupet, Safran, Sciences Computers Consultants et Transvalor. n
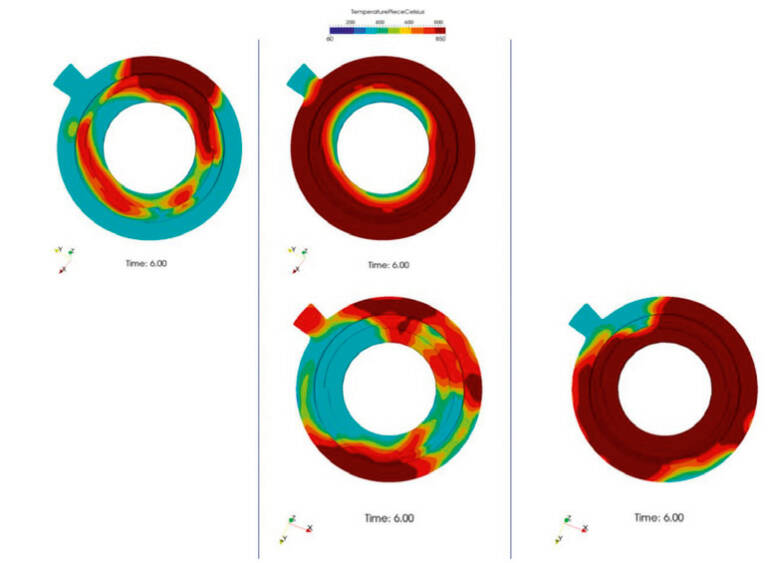
Figure 14 : Contour de température en surface, 6 secondes après l’immersion, pour les cas A (gauche), multi-charges (centre) et B (droite).
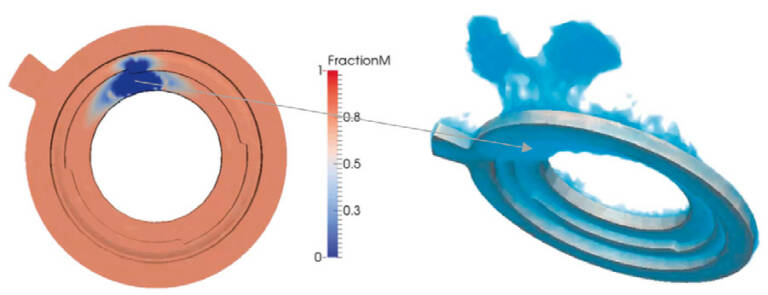
Figure 15 : Cas A – Fraction de phase martensitique à la surface de la pièce, 9 secondes après l’immersion (à gauche) ; mise en évidence de l’accumulation de vapeur dans la même zone (à droite).
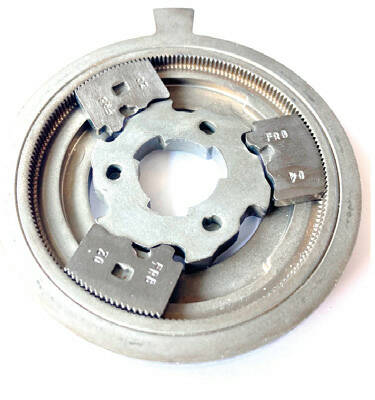
Figure 1 : Pièces typiques d’un mécanisme de dossier de siège nécessitant un traitement thermique. Diamètre extérieur : ~ 80 mm
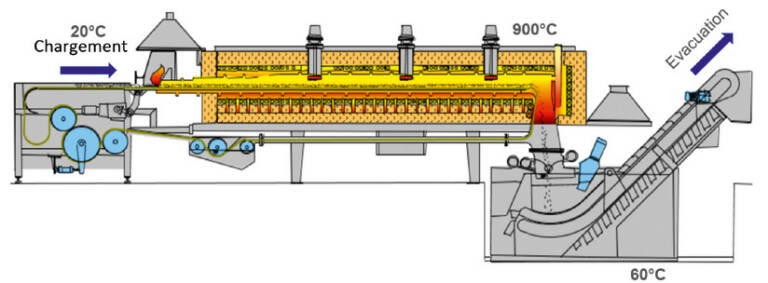
Figure 2 : Chaîne de carbonitruration standard (crédit : SAFED).
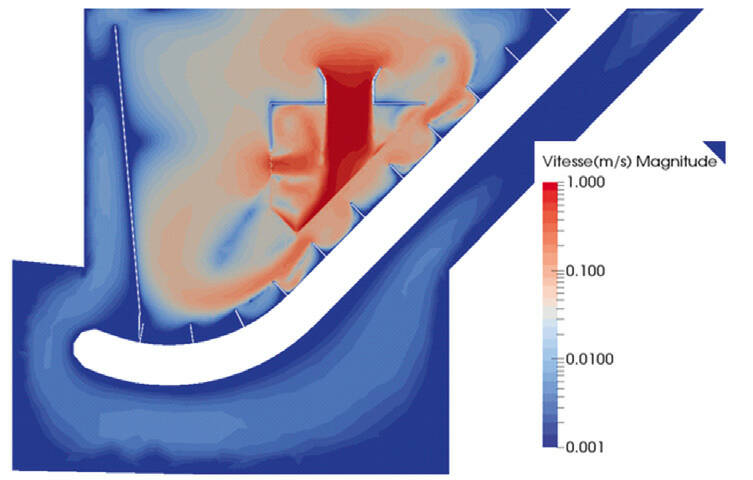
Figure 3 : Vitesse d’écoulement de l’huile dans le réservoir de trempe.
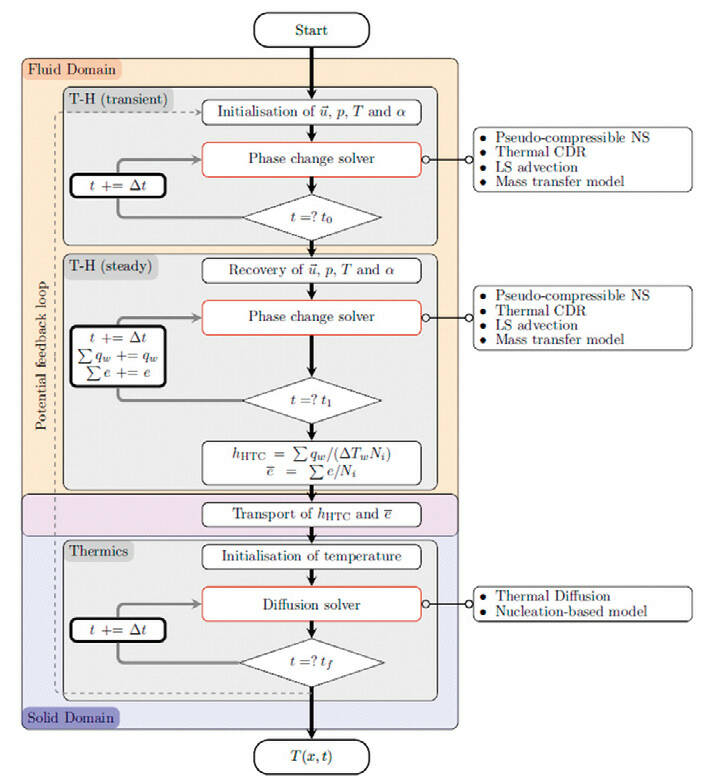
Figure 4 : Algorithme de résolution pour la trempe[4].
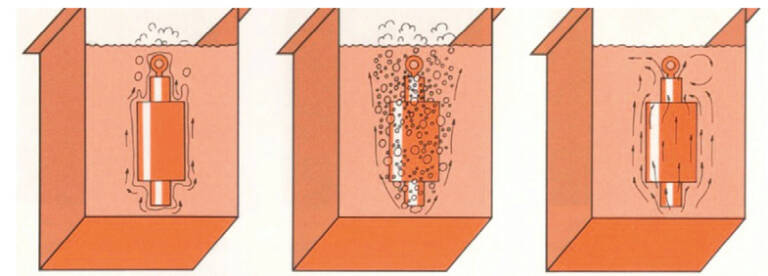
Figure 5 : Illustration des trois étapes de la trempe : caléfaction, ébullition nucléée et convection[9].
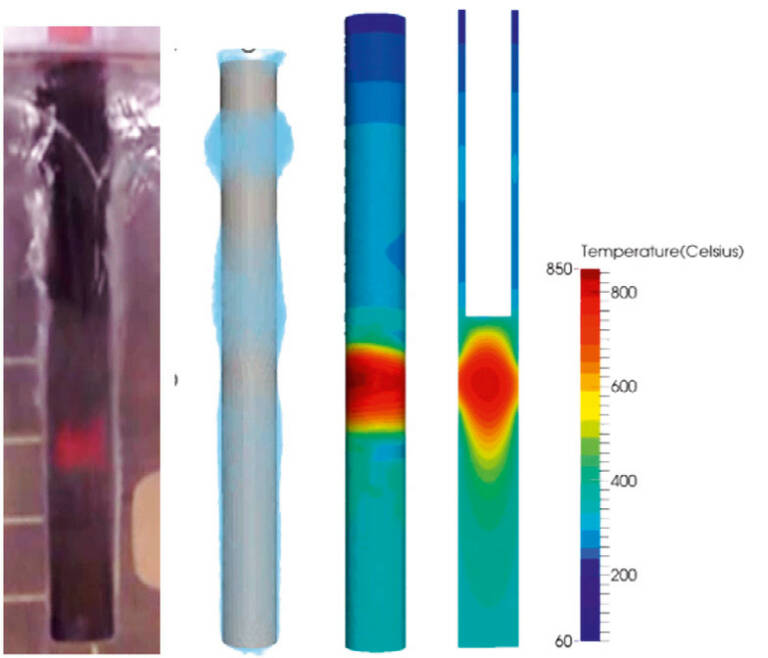
Figure 6 : de gauche à droite : test de drasticité à 9 secondes après l’immersion, simulation correspondante du film de vapeur, simulation de la température de surface, simulation de la température (section transversale).
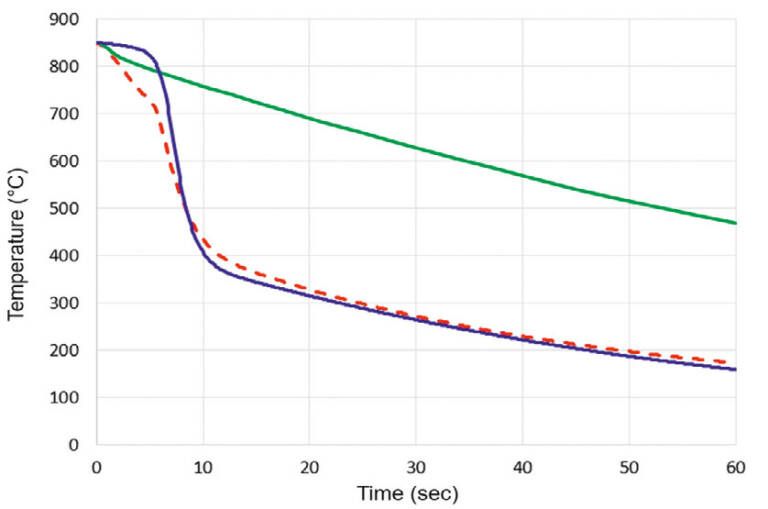
Figure 7 : Comparaison entre le test de drasticité expérimental (rouge), la simulation avec qobeo® sans modèle d’ébullition (vert) et avec modèle d’ébullition (bleu).
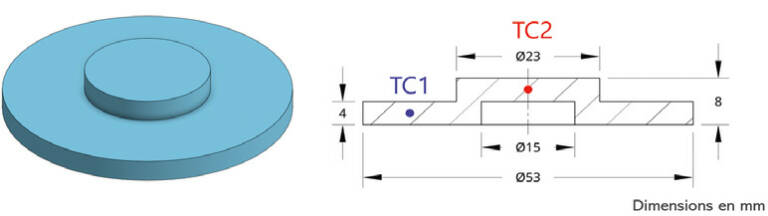
Figure 8 : Pièce simple avec semi-découpe, en vue isométrique (à gauche) et en coupe transversale (à droite). TC1 et TC2 sont deux capteurs de température dans le modèle de simulation.
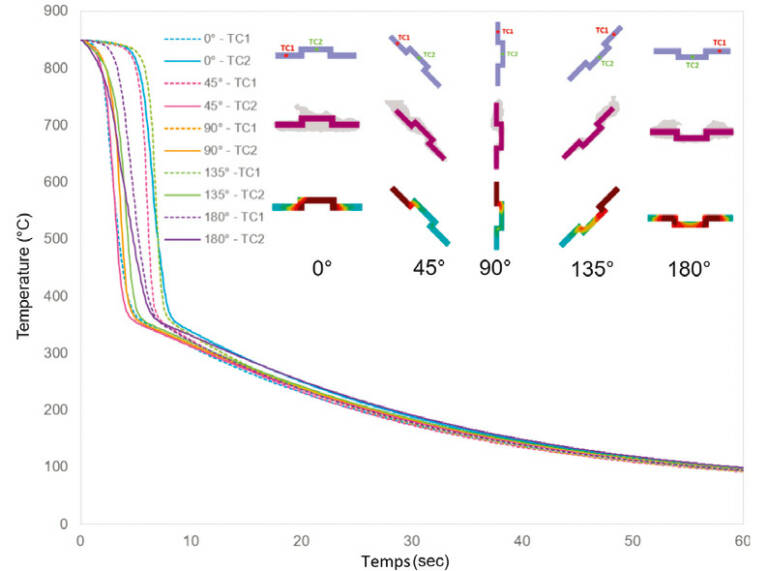
Figure 9 : Résultats de la simulation. Les images illustrent le film de vapeur et le gradient de température 4 secondes après l’immersion.
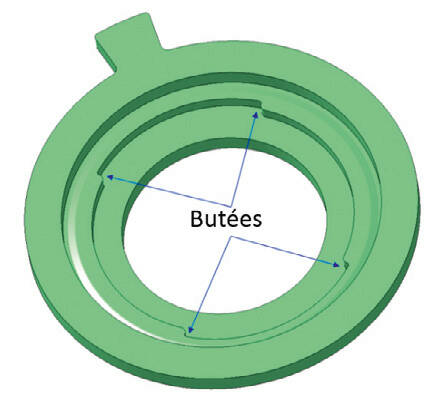
Figure 10 : Flasque mobile d’un mécanisme de dossier de siège. Mise en évidence des butées.
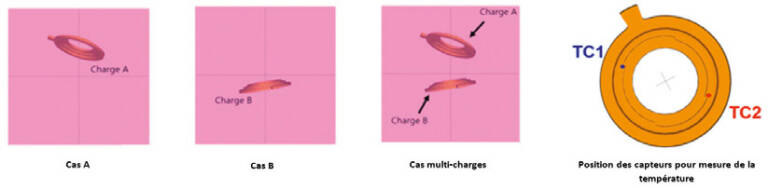
Figure 11 : Cas étudiés et emplacement des capteurs.
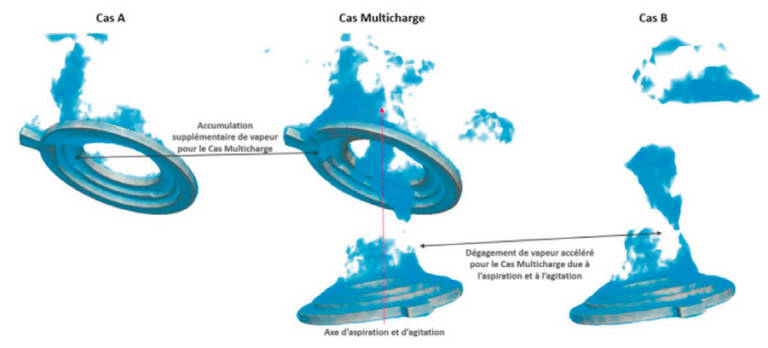
Figure 12 : Capture d’écran du flux de vapeur dynamique. Mise en évidence de plusieurs effets remarquables.
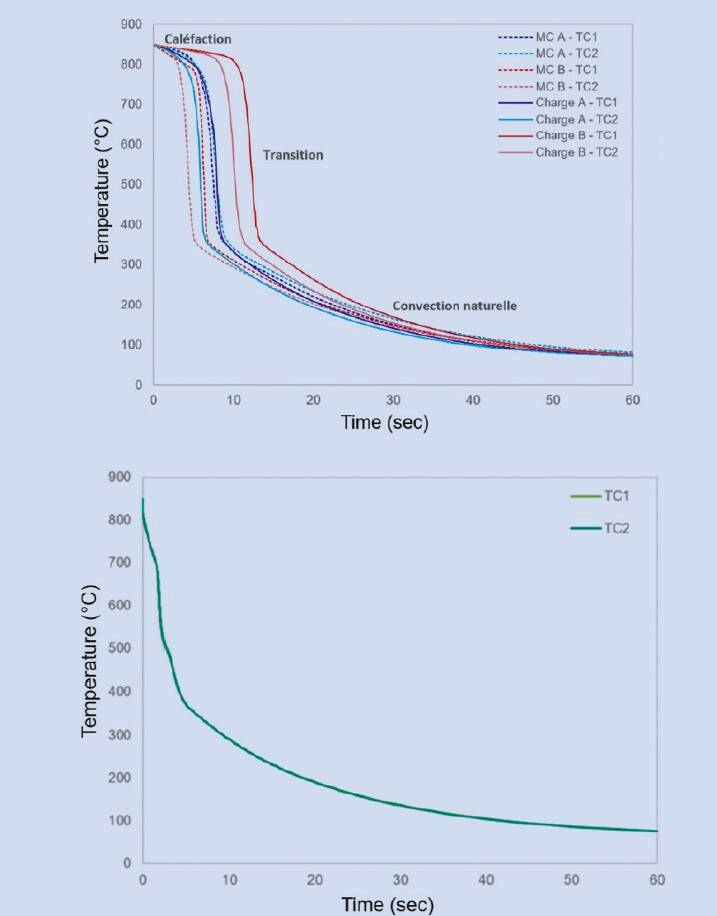
Figure 13 : Courbes de refroidissement avec qobeo® en haut) et l’approche classique HTC (en bas)