Optimisation d’un revêtement Nicrofer 6025 par projection thermique
Par Geoffrey DARUT ICB PMDM UMR 6303, CNRS, Université de Bourgogne Franche-Comté, UTBM, Belfort, Franc
Les superalliages à base de nickel sont utilisés dans de nombreux domaines industriels, tels que l’aérospatiale, l’énergie, l’automobile en raison de leur résistance élevée et de leurs bonnes propriétés mécaniques[1]. Parmi ces différents superalliages, l’Inconel 718 et l’Inconel 625 sont très étudiés notamment sous forme de revêtements par projection thermique.
1. Introduction
Le traitement de surface par voie sèche se fonde sur le traitement cinétique et thermique de particules injectées (poudre) ou générées par l’atomisation de fil dans une source de chaleur. Ces particules impactent sur la surface d’une pièce pour la revêtir afin d’améliorer ses performances fonctionnelles (barrière thermique, résistance à l’usure, à la corrosion, etc.) ou depuis quelques temps pour prolonger sa durée de vie (rechargement). Les principaux procédés utilisés pour la réalisation des revêtements base nickel sont la projection plasma sous air[2], la projection flamme haute vitesse HVOF[3] et la projection à froid / Cold Spray[4]. Outre les inconels, les matériaux de type MCrAlY, comme le NiCrAlY, font partie de la liste des superalliages base nickel étudiés notamment en aéronautique pour des applications de résistance à l’oxydation en tant que sous couche pour les barrières thermiques[5].
2. Contexte de l’étude
Dans le cadre d’une étude se rapportant au domaine de l’énergie, un nouveau matériau type superalliage base nickel a été investigué : le Nicrofer 6025. Ce matériau n’a jamais été cité dans la littérature scientifique de la communauté de la projection thermique. Il s’agit donc d’un premier développement d’un revêtement avec cet alliage. La base principale est de type NiCr comme les autres superalliages cités précédemment. Il s’agit à présent de trouver le procédé adéquat pour respecter le cahier des charges du revêtement. Dans ce cas précis, ce dernier doit être dense et le plus pur possible (faible oxydation). Les différents procédés de projection thermique se différencient par des sources thermiques différentes (plasma, flamme, arc électrique) en termes de températures et vitesses des flux gazeux. Il en résulte alors des propriétés différentes des particules comme le schématise la figure 1. Ces deux propriétés conditionnent leur état de fusion, leur réactivité avec l’atmosphère environnant (projection sous air ou gaz neutre) et leur déformation à l’impact sur le substrat à revêtir. Ce choix est donc très important, en plus des caractéristiques de la poudre à utiliser.
3. Développement des revêtements de Nicrofer 6025
Cette étude de développement d’un revêtement Nicrofer 6025 s’est donc intéressée à comparer 3 types de procédés de projection : plasma sous air (APS), plasma sous atmosphère contrôlé (VPS) et flamme haute vitesse (HVOF). Pour les différents revêtements obtenus, les caractérisations menées consistent en l’observation des microstructures par microscopie électronique puis la mesure de la porosité et de l’oxydation par analyse d’image.
3.1 Matériau et procédés
La poudre spécifique de ce superalliage Nicrofer 6025 n’est pas disponible sur catalogue chez les fournisseurs de matériaux pour la projection thermique. Elle a donc été élaborée chez un partenaire pour répondre à la demande. La microstructure et les propriétés des revêtements dépendent de différents paramètres et notamment la qualité de la poudre utilisée (morphologie, granulométrie, composition) en lien avec le procédé de fabrication. Des poudres équivalentes en termes de composition chimique et distribution granulométrique mais de morphologie différente peuvent conduire à des revêtements aux propriétés différentes. Les particules plutôt anguleuses sont généralement denses alors les particules sphériques peuvent être denses ou poreuses. Il en résulte des densités différentes modifiant les trajectoires des particules et les histoires thermiques (conductivité et diffusivité) durant leur parcours dans le jet de projection. Enfin, la coulabilité de la poudre est primordiale. Si elle est mauvaise, le débit massique ne sera pas constant ; ce qui est néfaste à la qualité du revêtement. C’est pourquoi le procédé de fabrication de la poudre a été l’atomisation gazeuse afin d’avoir une poudre sphérique de très bonne coulabilité. Afin de travailler avec les différents procédés APS et HVOF, une granulométrie de 22-46 µm a été sélectionnée. La figure 1 présente la morphologie de la poudre obtenue et utilisée pour la réalisation de tous les revêtements.
Les procédés de projection sont montés sur des robots pour travailler dans une cabine fermée en sécurité et pour réaliser des trajectoires bien précises. En projection thermique, la surface d’une pièce sera revêtue de façon homogène si un certain pas de projection est respecté. Ce dernier correspond au décalage progressif du jet de particules afin de couvrir la surface. Le pas doit être constant et dépend du procédé utilisé (répartition/divergence du jet de projection) et de la dimension des particules qui vont venir impacter la surface.
La première technologie de projection utilisée est la flamme haute vitesse HVOF au travers de deux procédés : un appartenant à la catégorie dite « gas fuel » le Diamond Jet (Oerlikon Metco) et l’autre de la catégorie « liquid fuel » l’eGun (Flame Spray Technologies). La différence globale réside en la température de la flamme et la pression dans la chambre de combustion du pistolet. Les particules injectées seront alors chauffées à des températures différentes et auront également des vitesses différentes. Pour chacun des procédés, les caractéristiques des particules pourront aussi être modifiées en changeant les débits des gaz/liquide formant la flamme. Le tableau 1 présente les paramètres de projection des procédés HVOF. Pour le Diamond Jet, deux types de buses sont disponibles qui permettent d’obtenir une flamme plus ou moins chaude. La flamme se forme par réaction de l’oxygène et du méthane. Pour l’eGun, l’oxygène et l’éthanol forment la flamme. Ce dernier a été sélectionné car, comparé aux autres procédés HVOF, l’utilisation de l’éthanol en remplacement des autres combustibles (méthane, acétylène, kérosène, etc.) est moins impactant sur l’environnement. Ce procédé représente un progrès très récent dans la technologie HVOF à combustible liquide. L’éthanol présente des caractéristiques respectueuses de l’environnement et génère donc moins d’émission (dioxyde de carbone) que les combustibles liquides fossiles conventionnels. La volonté de rendre la projection thermique plus « verte » doit être enclenchée. Ce domaine se développe de plus en plus avec la conscience de diminuer son empreinte énergétique que ce soit sur la consommation et le type de matière première, le rendement de projection, etc.
La seconde technologie de projection utilisée est le plasma au travers de deux procédés : sous air (APS) avec une torche dite à cascade ou segmentée Sinplex Pro (Oerlikon Metco) et sous atmosphère contrôlé (VPS) avec une torche PTF4 (Oerlikon Metco). La première différence entre ces deux procédés est l’environnement de travail. Sous air, les particules sont en contact avec l’oxygène avec lequel elles peuvent réagir du fait de leur état de fusion. Il en résulte une oxydation à la périphérie de ces particules pendant leur trajet en vol pendant la projection. Une seconde oxydation se produit en surface du revêtement en cours de construction entre chaque passage successif de la torche plasma pour construire les différentes couches successives pour croître en épaisseur. La température du substrat ou de la pièce peut atteindre des températures entre 50 et 500 °C en fonction de l’inertie de la pièce, de sa dimension, de la distance par rapport au procédé, des systèmes de refroidissement mis en place etc. L’utilisation d’une atmosphère contrôlée dans une enceinte où le vide est fait, pour remplacer l’air par un gaz neutre non réactif à savoir l’argon, permet d’empêcher l’oxydation. Le revêtement obtenu est alors pur. En revanche il s’agit d’un procédé beaucoup plus complexe comprenant l’enceinte sous vide, plusieurs groupes de pompage, des systèmes de refroidissement complémentaires pour le robot et les parois. Le coût de fabrication du revêtement est plus important, mais en contrepartie, la pureté, la densité et l’adhérence sont supérieures au même dépôt APS sous air. Concernant la projection plasma APS, une torche plasma dite à cascade est utilisée. Elle se différencie des autres torches plasma standard de type PTF4 par une construction avec des parties isolantes permettant un arc électrique plus long (tension plus grande) et surtout plus stable. Une puissance plus faible et des débits de gaz secondaires réduits (50 à 80 % pour l’hydrogène) sont nécessaires pour faire fondre les matériaux et produire des revêtements. Le tableau 2 présente les paramètres de projection importants. Les plasmas sont de base argon avec ou sans hydrogène, avec des puissances de 21 à 48 kW.
La figure 2 présente des images de la projection de particules sur les substrats avec les procédés APS, HVOF et VPS. Les différences principales entre ces procédés utilisés sont listées dans le tableau 3. Pour résumer, les particules sont plus rapides avec le procédé HVOF ; ce qui limite le temps de vol de ces particules et la possibilité de réaction avec l’air environnant qui engendre l’oxydation finale du revêtement. Également, la flamme est moins chaude que le plasma. Le procédé VPS permet de s’affranchir de l’air autour du jet de projection. Le procédé plasma APS est le plus versatile en termes de matériaux pouvant être projetés.
Des plaquettes rectangulaires 20*50*1,5 mm en acier inoxydable sont utilisés pour réaliser les essais paramétriques. Au préalable, un dégraissage à l’éthanol puis un sablage de la surface avec du corindon sont effectués.
3.2 Microstructure des revêtements HVOF
La figure 3 présente les microstructures des revêtements obtenus avec les deux procédés HVOF. Ils sont tous très denses, mais contiennent plus ou moins d’oxydes observables par microscopie optique ou électronique. Les zones oxydées apparaissent sur ces clichés en gris sombre. Le degré d’oxydation dépend des propriétés de la flamme HVOF (température, stœchiométrie notamment). Pour le procédé Diamond Jet (DJ), les paramètres étudiés sont la buse utilisée, les débits d’air, d’oxygène et de méthane. En comparant DJ1 et 2, l’utilisation d’une buse permettant une flamme plus froide, réduit la quantité d’oxyde présente dans le revêtement. En diminuant le débit volumique de méthane et d’oxygène, l’oxydation est à nouveau réduite (DJ3). Concernant le procédé eGun (Eg), les paramètres étudiés sont les débits d’éthanol et d’oxygène. D’une façon générale, la quantité d’oxydes est bien plus faible (moins de zones grisées). Le premier jeu de paramètres permet d’obtenir un revêtement très dense faiblement oxydé (Eg9). En augmentant les débits des fluides, l’oxydation augmente (Eg10 puis Eg11). L’oxydation est la plus petite pour de faibles valeurs du débit d’oxygène et surtout d’éthanol.
Plasma
Dans le cas de la projection plasma atmosphérique APS (série S), les principaux paramètres étudiés sont l’utilisation du gaz diatomique hydrogène comme gaz secondaire du plasma et l’intensité du courant d’arc. La conductivité thermique des plasmas thermiques est d’une importance primordiale car elle contrôle les pertes d’énergie dans l’arc ainsi que le transfert de chaleur vers les matériaux des particules injectées. Un faible ajout d’hydrogène entraîne une forte augmentation de la tension d’arc et de l’efficacité de la torche. Également, la conductivité thermique augmente avec le pourcentage volumique d’hydrogène dans un mélange argon-hydrogène. Par exemple, avec 30 % d’hydrogène en volume, la conductivité thermique du mélange est multipliée par 12[6]. Concernant le courant d’arc, des valeurs plus élevées entraînent des températures et des vitesses de particules plus importantes avec l’augmentation de la puissance. En choisissant le procédé de plasma sous air, le risque d’oxydation est réel compte tenu de la haute température du plasma comparée à la flamme précédente (cf. figure 1). Ce risque est d’autant plus important que les vitesses des particules sont plus faibles. C’est pourquoi le débit maximal d’argon a été sélectionné à hauteur de 100 l/min. La torche segmentée utilisée est encore peu étudiée et répandue dans le domaine de la projection thermique. Elle a donc été intégrée à cette étude pour voir le potentiel à haut débit de gaz plasmagène.
La figure 4 présente les microstructures des revêtements APS. La diminution de la valeur de l’intensité du courant, qui se traduit par une diminution de la puissance du plasma, induit une réduction des zones oxydées (S4→S6→S7 et S5→S9). L’augmentation du débit d’hydrogène augmente également la présence des oxydes (S7→S8). Quels que soient les revêtements, la porosité est bien inférieure à 1 %. Concernant le procédé VPS, les microstructures des revêtements présentées sur la figure 5 démontre bien la forte densité et l’absence d’oxydation. La variation des paramètres tant en valeur de débit d’hydrogène qu’en intensité du courant d’arc n’influence pas la microstructure. Un effet qui n’a pas été étudiée sur cette étude pourrait être le rendement de projection, c’est-à-dire la part des particules qui sont injectées dans le plasma (débit massique de poudre sortant du poudrier) et qui participent à la construction du revêtement (masse déposée). Pour un débit massique constant, choisir une puissance de torche trop importante ne permet pas d’améliorer encore ce rendement de projection. Si la puissance fournie par le plasma est en effet trop importante par rapport à celle nécessaire à la fusion des particule, le risque de vaporisation du matériau augmente avec une perte de rendement associée. Actuellement, la recherche de la montée en puissance des torches est investiguée afin d’injecter des masses de poudre plus importantes dans le plasma afin de diminuer les temps de projection et gagner en productivité.
3.3 Propriétés des revêtements
Les microstructures des revêtements ont été analysées quantitativement afin de comparer les échantillons les uns par rapport aux autres et confirmer les observations visuelles menées. Les valeurs de porosité microscopique ainsi que le pourcentage d’oxydation ont été déterminés à partir de clichés photographiques pris au microscope électronique avec un grossissement et une résolution adaptée à l’échelle des éléments de la microstructure. La teneur en porosité et oxydation a été estimée par analyse d’images avec le logiciel Image J, en moyennant 5 clichés. La figure 6 présente les valeurs obtenues. Comme attendu, les revêtements VPS sont à la fois les plus denses (> 0,1 % de porosité) et les moins oxydés (> 0,1 % de porosité). Ensuite vient le procédé eGun avec l’essai (0,1 % de porosité et 0,2 % d’oxydation). L’étude aboutissant au revêtement sur une pièce technologique unitaire, le procédé VPS a été validé et choisi (cf. figure 7).
4. Conclusion
Cette étude a permis de comparer les microstructures de revêtements de base nickel de type Nicrofer 6025 obtenus par projection thermique. Deux familles de procédés flamme et plasma ont été investiguées. Ce matériau étant métallique, le principal risque est son oxydation. Également, la contrainte de haute densité du revêtement imposée par le cahier des charges a permis d’identifier les procédés flamme haute vitesse HVOF et le procédé plasma VPS. Le procédé APS a aussi été étudié avec une torche configuration cascade pour analyser son potentiel pour cette application.
Les revêtements obtenus sont tous très denses (porosité inférieure à 0,1 % jusqu’à 1,6 %) avec plus ou moins d’oxydation (inférieure à 0,1 jusqu’à 39,3 %). Pour les procédés HVOF, la flamme plus chaude du Diamond Jet (type « gas fuel ») induit la plus forte oxydation comparée à l’eGun (type « liquid fuel »). Le procédé plasma VPS est le seul permettant d’obtenir un revêtement dense et sans oxydation. Il a donc été choisi pour réaliser le revêtement final sur la pièce technologique. Le procédé eGun pourrait également être choisi pour son plus faible coût de fabrication de revêtement dans le cadre de revêtements à plus grande échelle.
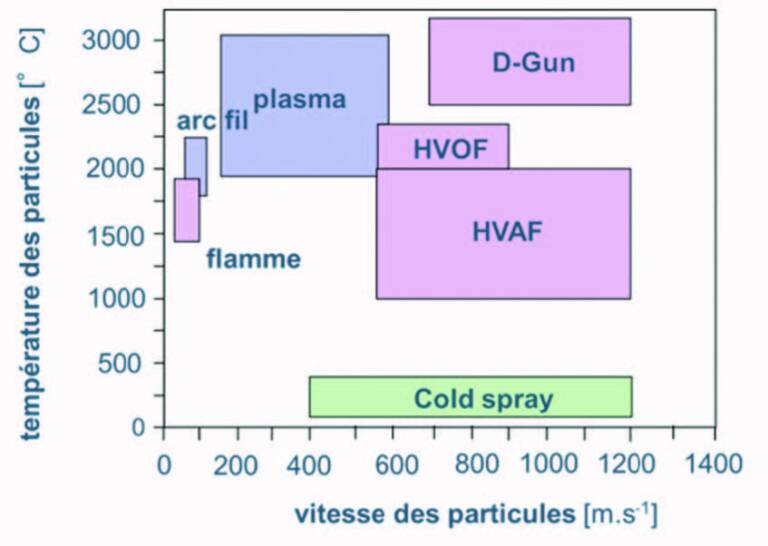
Figure 1 a: Répartition schématique des procédés de projection thermique en termes de vitesses et températures des particules
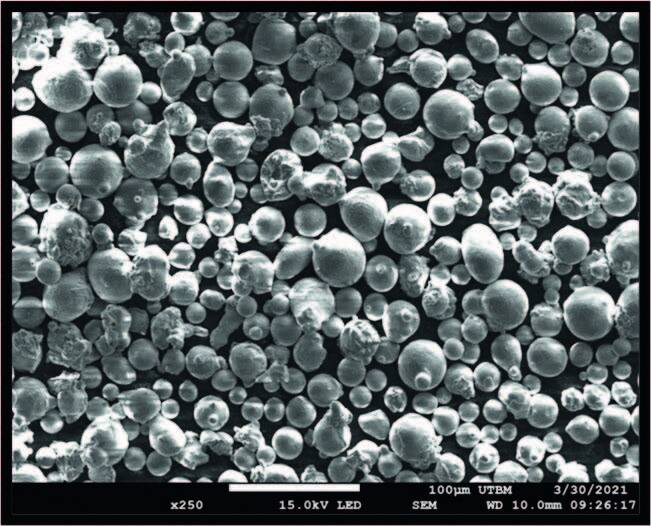
Figure 1b. Microstructure de la poudre Nicrofer 6025
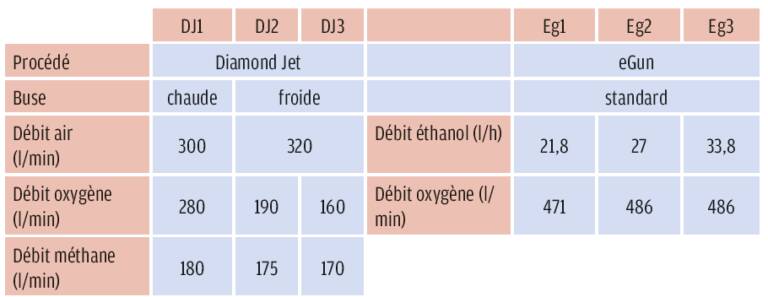
Tableau 1. Paramètres globaux des procédés HVOF
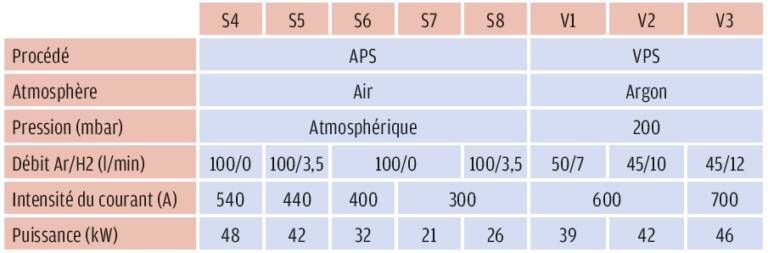
Tableau 2. Paramètres globaux des procédés APS et VPS
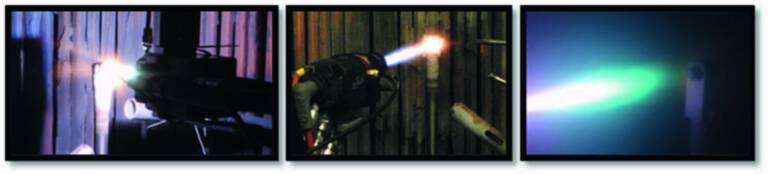
Figure 2. Clichés photographiques des procédés APS, HVOF et VPS (de gauche à droite)
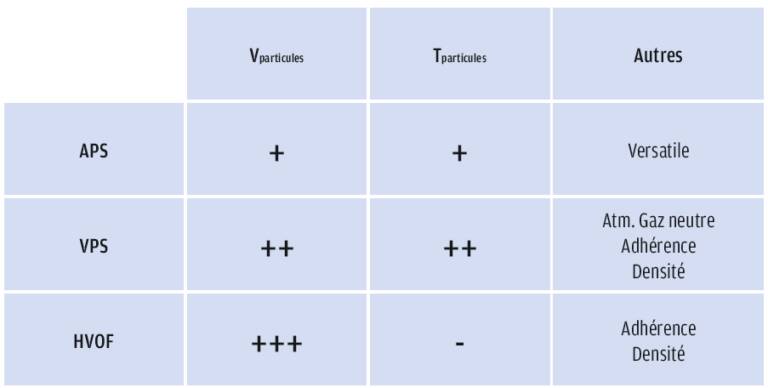
Tableau 3. Principales caractéristiques vitesse/température des particules des procédés APS, VPS et HVOF.
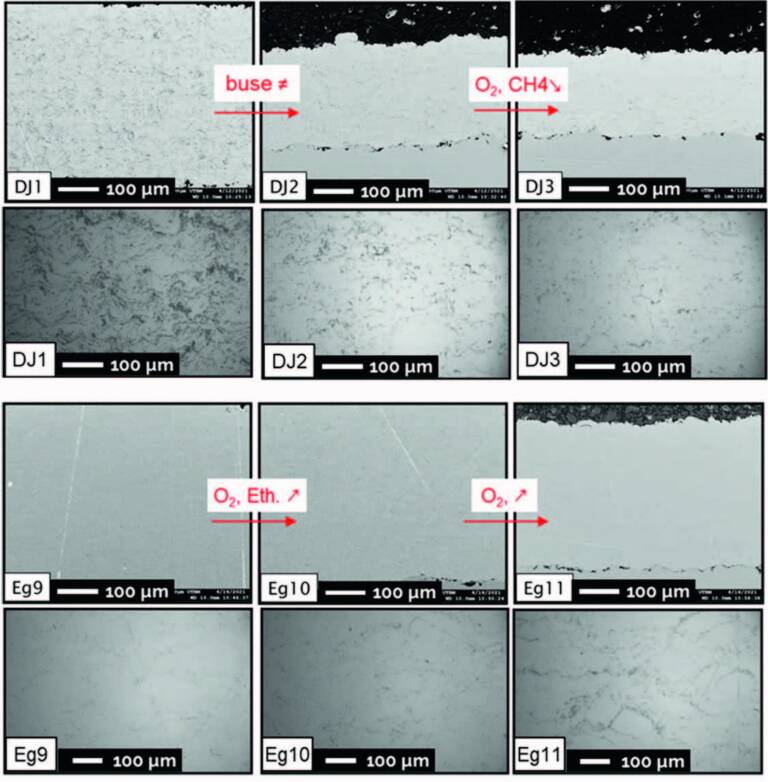
Figure 3. Microstructures de revêtements HVOF avec les procédés Diamond Jet (DJ) et eGun (Eg)
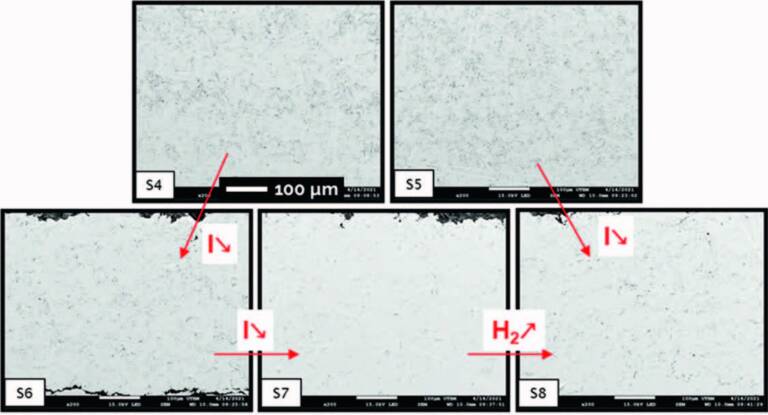
Figure 4. Microstructures de revêtements APS (S) avec les effets de la variation de l’intensité du courant I et du débit du gaz hydrogène H2
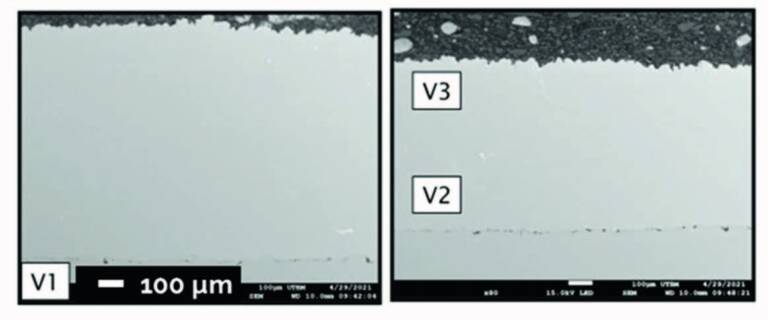
Figure 5. Microstructures de revêtements VPS (V)
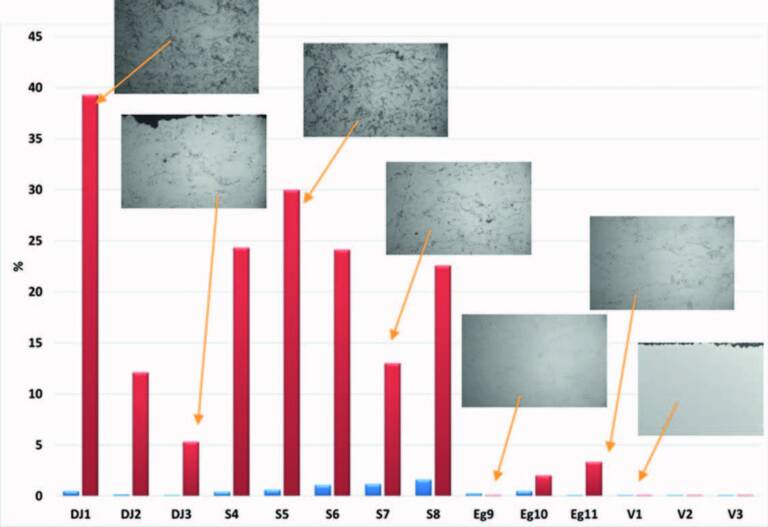
Figure 6. Pourcentages d’oxydation (rouge) et de porosité (bleu) des revêtements HVOF Diamond Jet (DJ) et eGun (Eg), plasma APS (S) et VPS (V)
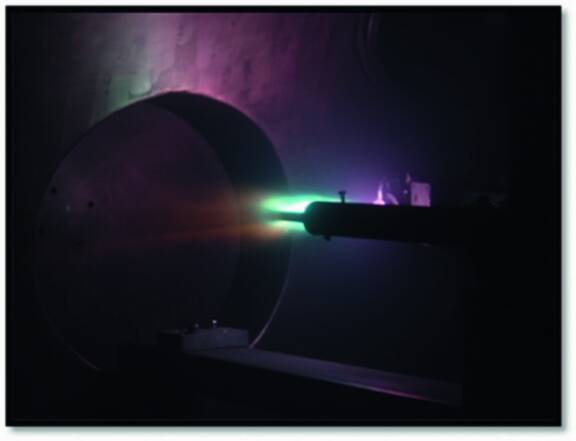
Figure 7. Application du revêtement NiCroFer 6025 sur pièce industrielle par le procédé plasma VPS
Bibliographie
[1] G. Jangali Satish, V.N. Gaitonde, and V.N. Kulkarni, Traditional and Non-Traditional Machining of Nickel-Based Superalloys : A Brief Review, Mater. Today Proc., 2021, 44, p 1448–1454.
[2] Z. Zhang, D.H.L. Seng, M. Lin, S.L. Teo, T.L. Meng, C.J.J. Lee, Z.-Q. Zhang, T. Ba, J. Guo, K. Sundaravadivelu, P.K. Aw, and J. Pan, Cold Spray Deposition of Inconel 718 in Comparison with Atmospheric Plasma Spray Deposition, Appl. Surf. Sci., 2021, 535, p 147704.
[3] J. Tuominen, P. Vuoristo, T. Mäntylä, M. Kylmälahti, J. Vihinen, and P.H. Andersson, Improving Corrosion Properties of High-Velocity Oxy-Fuel Sprayed Inconel 625 by Using a High-Power Continuous Wave Neodymium-Doped Yttrium Aluminum Garnet Laser, J. Therm. Spray Technol., 2000, 9(4), p 513–519.
[4] D. Shrestha, F. Azarmi, and X.W. Tangpong, Effect of Heat Treatment on Residual Stress of Cold Sprayed Nickel-Based Superalloys, J. Therm. Spray Technol., 2022, 31(1), p 197–205.
[5] P. Sokolowski, T. Kielczawa, R. Musalek, T. Tesar, and M. Nowakowska, The Behavior of Plasma Sprayed Thermal Barrier Coating with Laser Microtextured Bond Coat under High Temperature Testing, Surf. Coat. Technol., 2023, 453, p 129095.
[6] P.L. Fauchais, J.V.R. Heberlein, and M.I. Boulos, “Thermal Spray Fundamentals : From Powder to Part,” (Boston, MA), Springer US, 2014, doi:10.1007/978-0-387-68991-3. Bibliographie