Traitements thermiques localisés
Par Guy Murry, Ingénieur-consei
Par traitements thermiques localisés, il faut entendre ceux conférant aux aciers des propriétés particulières au voisinage de leur surface. Deux grandes catégories peuvent être distinguées : le durcissement par trempe après chauffage superficiel et les traitements thermochimiques qui font intervenir des modifications de la composition du métal au voisinage de sa surface.
Nous nous intéresserons dans cet article à ceux qui ont pour objet d’améliorer les performances mécaniques des pièces sollicitées principalement au voisinage de leur surface et d’accroître ainsi, par exemple : leur performance mécanique en flexion et / ou torsion, leur endurance en flexion et / ou torsion, leur résistance à l’usure, leur tenue à la fatigue-roulement sous fortes charges. Et cela, tout en conservant à cœur une ductilité qui assure la sécurité du fonctionnement. Deux grandes catégories de traitements thermiques localisées peuvent être distinguées : le durcissement par trempe après chauffage superficiel et les traitements thermochimiques qui font intervenir des modifications de la composition du métal au voisinage de sa surface.
Le durcissement par trempe après chauffage superficiel
Cette technique, couramment appelée « trempe superficielle » permet d’obtenir en surface des duretés élevées et de générer des contraintes résiduelles favorables, tout en conservant à la sous-couche une bonne ténacité. Ces résultats sont obtenus en n’austénitisant que la zone que l’on veut durcir. De ce fait, il faut limiter le plus possible la conduction de la chaleur dans la masse du métal et donc écourter le chauffage. Plus ce dernier sera rapide et plus l’on maîtrisera la profondeur de la couche durcie. Les moyens de chauffage utilisables dans ces conditions seront ceux qui développeront les plus grandes puissances surfaciques. On peut citer le chalumeau (qui a été historiquement le premier moyen de chauffage utilisé), l’induction à moyenne ou haute fréquence (le moyen le plus utilisé), la torche plasma, le faisceau laser, le faisceau d’électrons.
A l’exception de l’induction, les moyens utilisés sont empruntés aux soudeurs lesquels fournissent un paramètre de classement de leur efficacité avec la prise en compte de la puissance spécifique, à savoir :
Chalumeau : 100 à 300 W / cm²
Torche plasma : 500 à 104 W / cm²
Faisceau laser : 103 à 106 W / cm²
Faisceau d’électrons : 103 à 107 W / cm²
Le chauffage par induction et le chauffage par faisceaux d’électrons présentent l’avantage de générer la chaleur au sein même de la zone que l’on veut chauffer alors que les autres procédés exigent la surchauffe de la peau par laquelle transite toute la chaleur.
Les cycles thermiques en trempe superficielle
La couche superficielle des pièces traitées est portée à des températures supérieures à Ac3 (sur la totalité ou sur une partie de leur surface) au cours d’un chauffage rapide suivi d’un refroidissement énergique (au moyen de jets d’eau sous pression souvent) afin de limiter la conduction de la chaleur vers le cœur de la pièce. La figure 1 donne un schéma des cycles (chauffage par induction au défilé + refroidissement par jet d’eau) qui peuvent ainsi être réalisés au cours d’une même opération.
On voit que : Les chauffages sont rapides. Ils durent quelques secondes.
Les températures maximales atteintes décroissent quand la distance à la peau augmente. Les maintiens à la température maximale de chaque cycle sont absents ou très courts. Les refroidissements sont rapides (ils demandent quelques dizaines de secondes). Le gradient thermique change de sens au cours du refroidissement de telle sorte que la sous-couche est la dernière zone à revenir à la température ambiante.
Lorsque le chauffage fait appel à l’induction, il faut tenir compte des variations, avec la température, des propriétés magnétiques du fer et des aciers, variations qui modifient les conditions de chauffage :
Depuis la température ambiante jusqu’à la température de Curie (760 °c environ) pour le fer et les aciers non alliés à bas carbone (<0,47 % environ) ou jusqu’à la température de disparition de la ferrite, l’acier est ferromagnétique. De ce fait, la pénétration des courants induits et donc du chauffage est relativement limitée. Par exemple avec une fréquence de 4 kHz (moyenne fréquence), elle varie de 1 mm à 2,5 mm environ selon la puissance du générateur et avec une fréquence de 300 kHz (haute fréquence), elle varie de 0,1 mm à 1 mm environ selon la puissance du générateur.
Au-dessus de la température de Curie (760 °c environ) pour le fer et les aciers non alliés à bas carbone (<0,47 % environ) ou au-dessus de la température de disparition de la ferrite, l’acier est amagnétique. De ce fait, la pénétration des courants induits et donc du chauffage est plus importante. Par exemple avec une fréquence de 4 kHz (moyenne fréquence), elle peut atteindre 4 à 7 mm environ selon la puissance du générateur et avec une fréquence de 300 kHz (haute fréquence), elle peut atteindre 0,7 à 3 mm environ selon la puissance du générateur.
Les effets métallurgiques des cycles thermiques
Ils sont décrits par les documents suivants :
Diagrammes de transformations en chauffage continu pour ce qui concerne le chauffage. Diagrammes de transformation en conditions isothermes après chauffage rapide pour ce qui concerne le maintien en température. Diagrammes de transformation en refroidissement continu après austénitisation aux températures maximales de chaque cycle pour ce qui concerne les transformations au cours des refroidissements rapides ultimes.
Les transformations lors du chauffage
Les conditions de chauffage conduisent à prendre en compte un domaine particulier des diagrammes de transformation en chauffage continu, celui qui couvre les chauffages rapides et dans lequel, donc, les transformations sont reportées vers les plus hautes températures. La figure 2 donne un exemple de ces situations pour des vitesses de chauffage assez habituelles de l’ordre de 100 à 150° C/s. L’austénitisation devant permettre, dans la couche qui doit être durcie, de mettre tout le carbone en solution et de parvenir à une austénite homogène et à grains fins exigera qu’en surface le métal soit, dans l’exemple choisi, porté à une température égale ou supérieure à 1 000 °C mais inférieure à 1 070 °C environ (pour un grain d’indice 9). C’est le cas du cycle C1 décrit par la figure 1.
Dans l’épaisseur de la couche qui doit être durcie la température maximale atteinte est alors plus faible mais, à une faible profondeur, les conditions d’austénitisation restent satisfaisantes car :
la vitesse de chauffage un peu plus lente abaisse les exigences de température qui restent satisfaisantes,
la transition entre la fin du chauffage et le début du refroidissement peut être considérée comme équivalente à un très court maintien (ici de l’ordre de la seconde dans l’exemple choisi) dont le diagramme de transformation en conditions isothermes après chauffage rapide (voir exemple à la figure 3) décrit les effets. On voit que les températures limites peuvent être abaissées d’environ 20 à 30 °C. Cette évolution peut être sensiblement accentuée par un retard de douche.
Quand la profondeur augmente on constate que l’austénite, tout d’abord, n’est plus homogène (cas du cycle 2 de la figure 1), puis l’austénitisation n’est plus complète (Ac1d est franchie, Ac3d ne l’est pas). Enfin Ac1d n’est pas franchie et le métal n’est pas du tout austénitisé (cas des cycles C3, C4 et C5 de la figure 1). Si la température maximale atteinte est relativement élevée (cas du cycle C3) les carbures peuvent légèrement coalescer (ce qui provoquerait un léger adoucissement généralement insensible). Sinon, la structure du métal n’est pas modifiée (cas des cycles C4 et C5). Le tableau 1 décrit ces différentes situations. Enfin, il est indispensable de noter l’influence très importante de l’état initial de l’acier (et surtout de celui des carbures précipités) qui peut modifier très sensiblement les conditions d’austénitisation. En effet on constate que plus les structures initiales sont fines plus les températures limites maximales sont basses et, à contrario, plus les structures initiales sont grossières plus les températures limites maximales sont élevées. Le tableau 2 donne des indications concernant ces effets pour 2 nuances d’acier.
Les transformations lors de la trempe
Pour parvenir au résultat visé il est nécessaire que le refroidissement provoque une transformation martensitique dans la couche austénitisée. Les moyens de refroidissement utilisés ici (essentiellement des douches alimentées en eau sous pression) sont très efficaces car la multitude des petits jets empêche la formation de la couche de caléfaction et rend le refroidissement très énergique d’autant que le cœur du métal (qui n’a pas été échauffé ou très peu) absorbe aussi de la chaleur. Il est intéressant de remarquer que les lois de refroidissement ainsi réalisées se caractérisent par des valeurs du paramètre Dt700 / 300 qui sont de l’ordre de quelques secondes en surface des pièces et légèrement plus en profondeur aux limites de la zone qui se transforme. Dans ces conditions la trempabilité de l’acier traité a une influence particulière. On constate qu’elle n’intervient pratiquement pas si la profondeur durcie ne dépasse pas 2 à 3 mm. En effet, dans ces conditions même un acier peu trempant comme un acier C35 (DtM1 de l’ordre de quelques secondes) subit la transformation martensitique dans toute la couche austénitisée. Elle intervient par contre si la profondeur durcie doit dépasser 2 à 3 mm. Le refroidissement en profondeur n’est plus assez rapide et il est alors nécessaire de mettre en œuvre un acier un peu plus trempant et donc légèrement allié.
Le tableau 3 donne des ordres de grandeur des paramètres DtM des principaux aciers préconisés pour la trempe par induction ou au chalumeau. On constate que les trempabilités des aciers faiblement alliés mentionnés dans ce tableau sont excessives par rapport aux exigences du durcissement par trempe superficielle. On verra plus loin que ces niveaux de trempabilité sont parfois requis pour permettre de conférer à la masse du métal les propriétés mécaniques qui en feront un bon support de la couche durcie.
Les évolutions dimensionnelles
Les cycles thermiques auxquels l’acier est soumis dans la zone affectée par la chaleur créent des gradients thermiques très importants qui, comme le montre la figure 1, évoluent très rapidement. Ces gradients vont créer des gradients de dilatation, eux aussi très variables. La figure 4 donne, à titre d’exemple, une description des déformations linéaires accompagnant les cycles thermiques 1 et 3 présentés par la figure 1 (le cycle 1 correspond au métal voisin de la surface traitée alors que le cycle 3 décrit l’évolution thermique en un point de la zone affectée par la chaleur mais non austénitisée même partiellement). La figure 4 donne également une description de l’écart entre ces déformations linéaires relatives aux cycles thermiques 1 et 3 de la figure 1 (à noter qu’ici, lorsque cet écart est positif la peau est plus « longue » que la sous-couche et, au contraire, lorsqu’il est négatif la peau est plus « courte » que cette dernière). Cet exemple montre que l’on peut distinguer (selon les principes retenus dans les généralités relatives aux évolutions dilatométriques) quatre phases durant l’ensemble du traitement :
1. La première période (du temps to au temps t1) pendant laquelle la peau est plus longue que la sous-couche. Toute la zone austénitisée, bridée par la sous-couche ne peut que se déformer vers l’extérieur ce qui provoque un gonflement de la pièce. Cette phase cesse quand le début du refroidissement de la peau (en provoquant son retrait) recrée l’égalité dimensionnelle entre peau et sous-couche (temps t1).
2. La deuxième période (du temps t1 au temps t2) engendre un gradient important de dilatation, la sous-couche, se refroidissant plus lentement que la peau, est plus « longue » que cette dernière qu’elle soumet alors à un étirement. On fait ici l’hypothèse que la couche austénitisée (toujours à l’état austénitique) se déforme plastiquement sous cette action. Cette période s’achève (au temps t2) avec le début de la transformation martensitique le la zone austénitisée.
3. La troisième période (du temps t2 au temps t3) voit se développer la transformation martensitique de toute la couche austénitisée. On admet ici, pour simplifier, que les écarts de déformation sont encore accommodés par une déformation plastique. De ce fait on considère que tous les écarts dimensionnels ont été résorbés, jusqu’ici, par des déformations plastiques. Pour rendre compte de ces évolutions on translate verticalement la partie de la courbe décrivant l’évolution dimensionnelle de la couche au-delà du temps t3 jusqu’à annuler l’écart dimensionnel avec la sous-couche (au point O).
4. La quatrième période (au-delà du temps t3) voit apparaître un écart dimensionnel croissant entre couche et sous-couche qui, ici et compte tenu des hypothèses retenues, se traduit par une mise en compression élastique de la couche par la sous-couche. C’est ainsi que peuvent apparaître des contraintes résiduelles favorables à la tenue en fatigue.
Remarque : les déformations plastiques qui peuvent intervenir se manifestent dans la direction perpendiculaire à la surface de la couche trempée. Elles sont généralement considérées comme faibles (fait qui limite l’ampleur des usinages de finition). Mais il peut apparaître un autre mode de déformation lorsque la trempe est ici effectuée sur des pièces dans lesquelles subsistaient préalablement des contraintes résiduelles hétérogènes telles que celles engendrées par un dressage à froid. Lors du chauffage, ces contraintes sont plus ou moins relaxées et le métal tend à reprendre sa géométrie initiale.
Les propriétés mécaniques particulières
• La dureté
Il est généralement admis que la trempe après chauffage par induction provoque la formation d’une martensite plus dure (à teneurs en carbone identiques) que la martensite obtenue après austénitisation classique dans la masse et trempe. L’écart de dureté est souvent estimé être de l’ordre de 1 à 5 HRC. L’analyse des données disponibles semble montrer que cet écart varie avec la teneur en carbone ; quasiment nul si C % < 0,1, il atteint 3 HRC pour C % compris entre 0,4 et 0,5 % (voir figure 5), il diminue ensuite lorsque la trempe laisse subsister de l’austénite
résiduelle.
• La tenue à la fatigue
M. Martin indique qu’avec des aciers des types C38, C42, 42Cr2, 38B3 et 42B3 la limite d’endurance sD atteint les niveaux suivants :
Après recuit sD moyenne = 720 MPa.
Après trempe superficielle (HF - profondeur 1 mm) sD moyenne = 980 MPa.
Ce gain est attribué à l’action des contraintes résiduelles de compression dont E.D. Walker donne des ordres de grandeur estimés après trempe superficielle (HF) :
De - 650 à - 890 MPa aussi bien avec un acier non allié à 0,35 % C qu’avec un acier au bore à 0,35 % C.
De - 460 à - 560 MPa avec un acier non allié à 0,45 % C (niveaux plus faibles probablement dûs à une transformation martensitique incomplète, la température Mf étant trop basse).
Le revenu après trempe superficielle
Le revenu après trempe superficielle est défini comme un traitement effectué à une température de l’ordre de 150 à 250 °C (ou plus élevée si une dureté plus faible est recherchée). Il n’est pas systématiquement effectué mais on le réalise parfois pour d’une part diminuer la fragilité de la martensite formée en abaissant sa dureté et d’autre part relaxer les contraintes résiduelles.
La recherche d’une diminution de la fragilité de la martensite
A l’aide d’un essai spécifique (rupture par choc consistant à écarter deux dents d’un engrenage à l’aide d’un coin animé d’une certaine vitesse), les spécialistes de PSA ont mis en évidence, sur des aciers C35, C39 et C43, l’effet bénéfique d’un revenu qui permet d’éviter toute fissuration (alors qu’en l’absence de revenu et dans les mêmes conditions d’essai une dent se rompait).
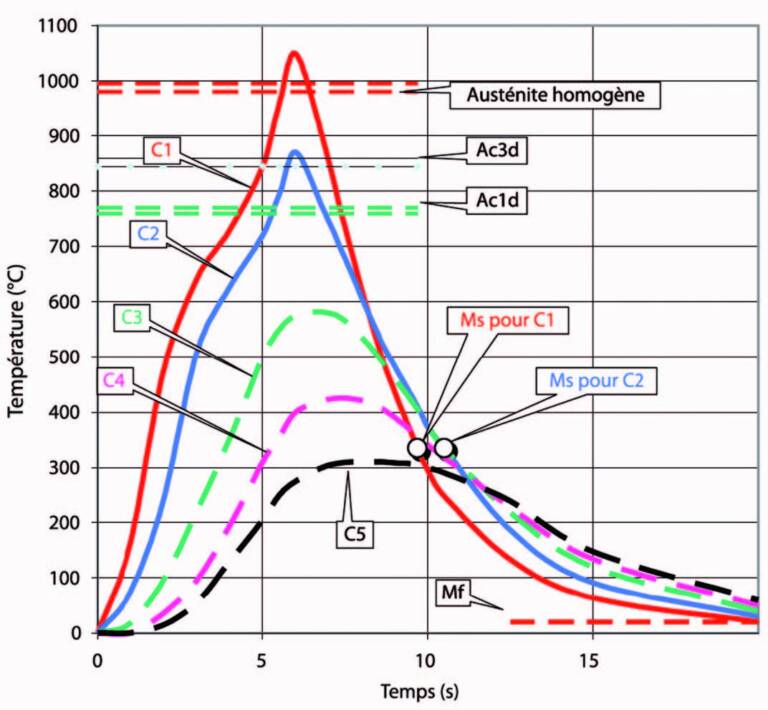
FIGURE 1 : Exemples de cycles thermiques
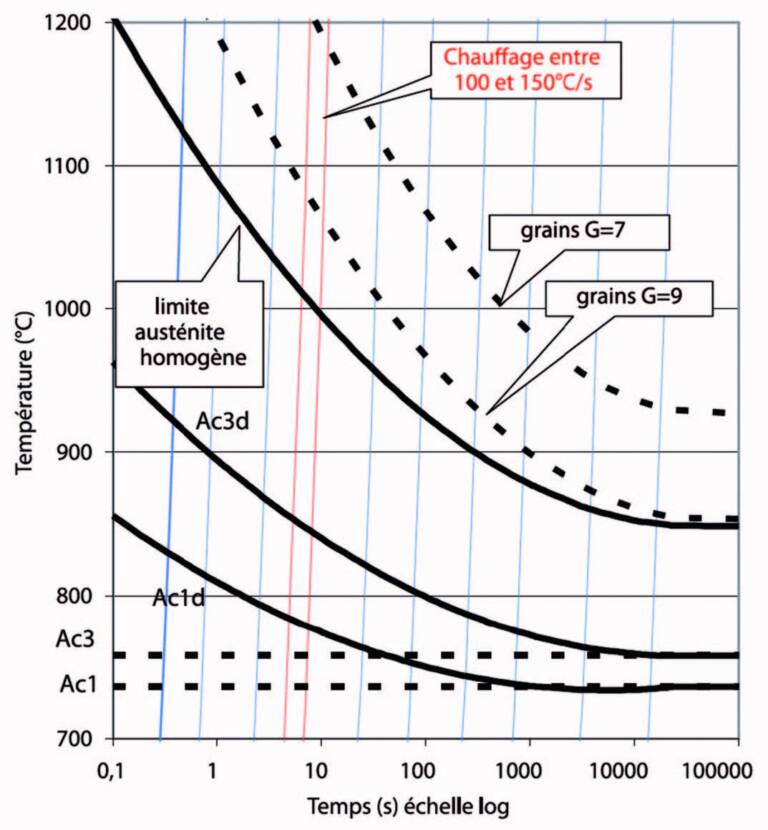
figure 2 : Schéma d’un diagramme de transformation en chauffage continu d’un acier 50CrMo4.
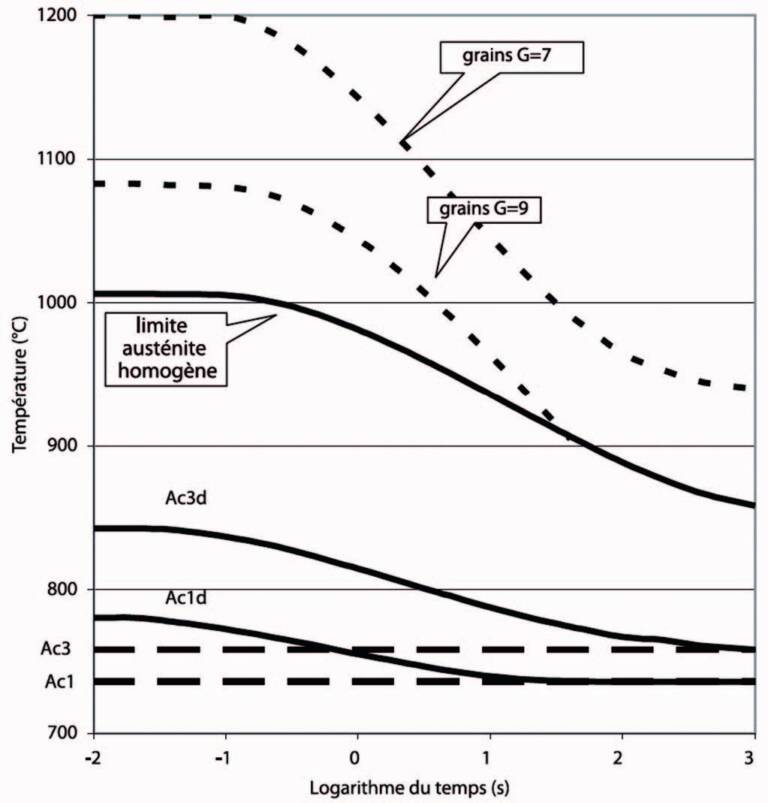
FIGURE 3 : Diagramme de transformation d’un acier 50CrMo4 en conditions isothermes (mise en température à 130°C/s).
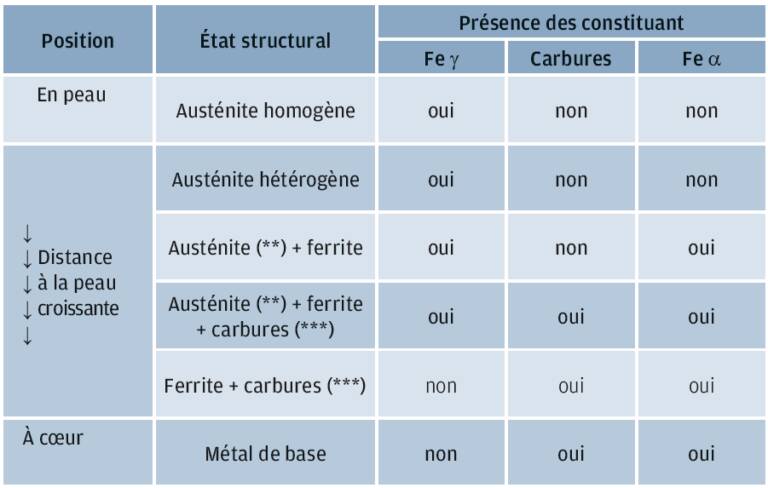
TABLEAU 1 : Description qualitative de l’état structural de la zone affectée par la chaleur à la fin du chauffage.
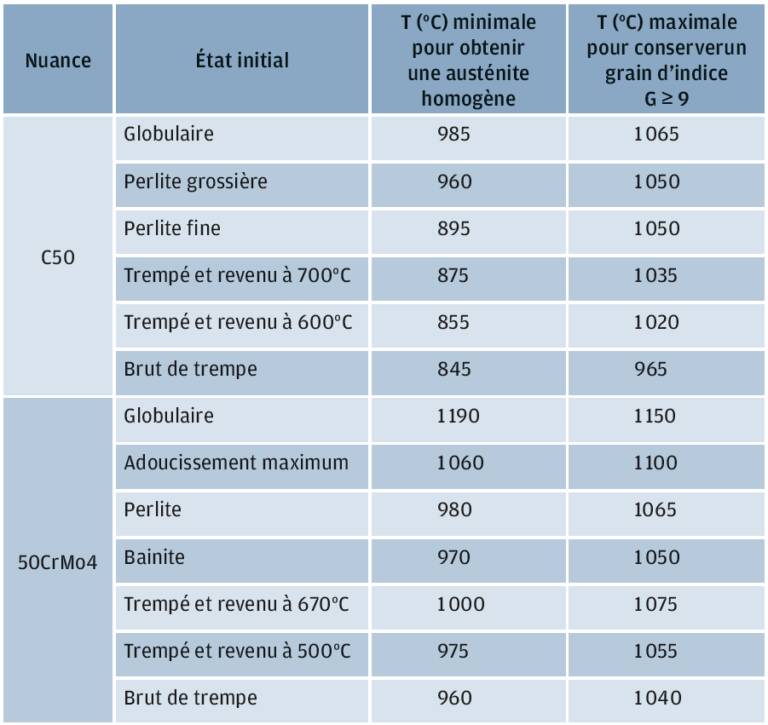
TABLEAU 2 : Conditions d’austénitisation en fonction de l’état structural initial.
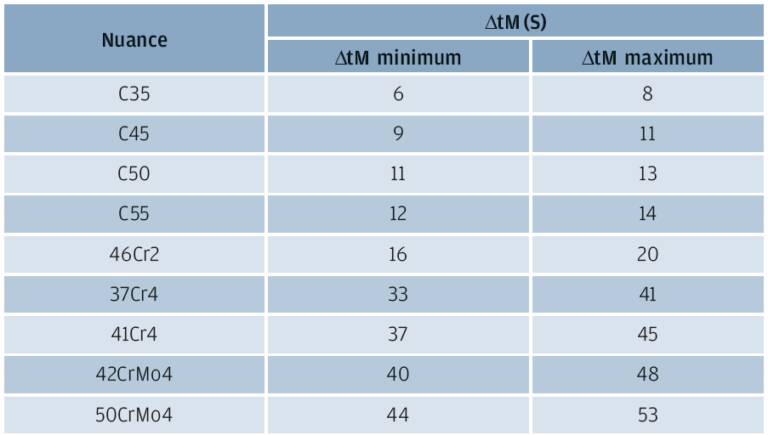
TABLEAU 3 : Ordres de grandeur des paramètres %t700/300 caractéristiques de la loi critique de transformation martensitique d’aciers préconisés pour la trempe par induction ou au chalumeau.
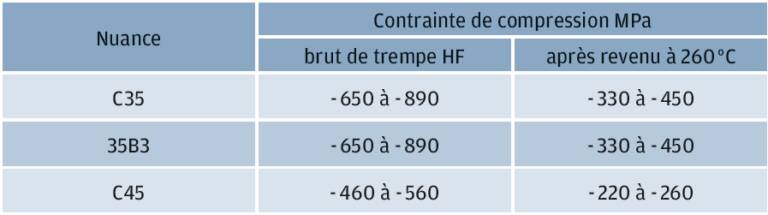
TABLEAU 4 : Ordres de grandeur des paramètres %t700/300 caractéristiques de la loi critique de transformation martensitique d’aciers préconisés pour la trempe par induction ou au chalumeau.
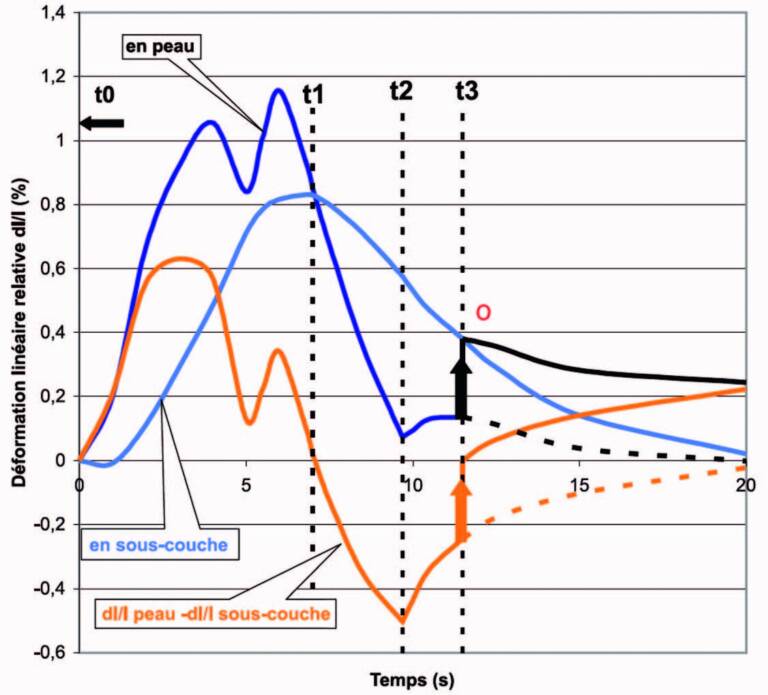
FIGURE 4 : Exemple des variations dimensionnelles relatives entre couche traitée et sous-couche.
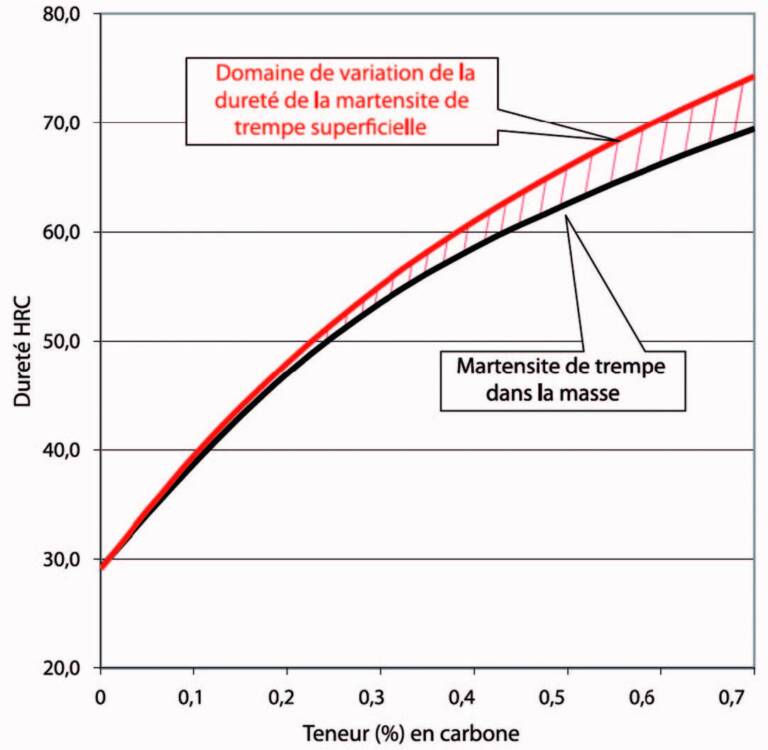
FIGURE 5 : Évolutions de la dureté de la martensite en fonction de la teneur en carbone après trempe dans la masse et après trempe superficielle.
Cet effet peut être attribué à une augmentation de l’énergie consommée par la rupture d’une dent (sur un acier 45Mn5 un tel revenu la fait passer de 15,3 à 46,6 J). Les conditions de revenu testées allaient de 3 heures à 180 °C (en four) à 1 min à 200, 220, 240, 260 ou 280 °C (par induction sans surchauffe de la peau de la pièce). Il faut noter que le revenu par induction plus court doit être réalisé à des températures plus élevées : l’équivalence entre température et durée du revenu peut se faire alors dans les conditions habituelles à l’aide du paramètre d’Hollomon et Jaffe qui s’écrit ici :
P = T [log(t) + 12420 – 6,5 HV]
En ce qui concerne les effets bénéfiques de ces revenus, il est aussi admis qu’ils contribuent à réduire les risques de fissuration lors d’une rectification ultérieure.
• La relaxation des contraintes résiduelles
Le tableau 4 rassemble des résultats relatifs à l’évolution des contraintes résiduelles générées par une trempe superficielle et partiellement relaxées par un revenu. Par ailleurs P.Rivat, A.Lombard, Y.Perrier et P.Romanelli ont montré qu’après trempe HF un revenu de 2 heures à 180 °C engendre une relaxation des contraintes résiduelles de surface de l’ordre de 45 à 55 %. Cette relaxation des contraintes résiduelles de compression engendrées par une trempe superficielle est essentiellement due à l’évolution dimensionnelle irréversible qui accompagne le revenu de la martensite et qui se manifeste, dans la couche trempée, par une contraction relative d’autant plus importante que ce dernier est réalisé à température plus élevée (mais néanmoins inférieure à 400 °C).
Cette contraction peut aller jusqu’à provoquer la création ou l’augmentation de contraintes de traction, comme l’ont montré P.Rivat, A.Lombard, Y.Perrier et P.Romanelli qui ont constaté qu’après un revenu par induction à une température trop élevée les contraintes résiduelles de surface sont devenues des contraintes de traction. Selon ces auteurs l’amplitude maximale de la contraction relative serait comprise entre 0,10 % (1e étape du revenu) et 0,33 % (revenu complet). Mais la relaxation, en diminuant les contraintes résiduelles de compression engendrées par une trempe superficielle, va à l’encontre de l’effet recherché sur la tenue à la fatigue. Ainsi M. Martin indique qu’avec des aciers des types C38, C42, 42Cr2, 38B3 et 42B3 la limite d’endurance sD passe de 980MPa après trempe HF (profondeur 1 mm) à 890 MPa après trempe HF et revenu à 230°C.
• Le choix du revenu
La trempe superficielle n’est pas systématiquement suivie d’un revenu. Dans bien des cas on conserve l’état brut de trempe réservant le revenu à température relativement basse (150 à 250°C environ) pour diminuer la fragilité de la couche durcie en cas de risque de rupture par chocs en service. En cas de sollicitations de fatigue en service on évitera dans la mesure du possible tout revenu susceptible de diminuer les contraintes résiduelles de compression présentes en surface.
Le choix de l’acier
Le choix de l’acier doit découler des considérations suivantes :
La couche durcie doit être dure ce qui impose une teneur en carbone assez élevée. On peut remarquer que la norme NF qui définissait les aciers spéciaux pour trempe après chauffage superficiel imposait que le minimum de la fourchette en carbone soit supérieur ou égal à 0,34 %.
La couche durcie doit être totalement martensitique : pour ce faire il ne doit pas subsister d’austénite résiduelle ce qui signifie que la température Mf de l’acier ne doit pas être inférieure à la température ambiante et donc que la température Ms ne doit pas être inférieure à 315 °C (ce qui, pour un acier non allié, impose C % < 0,5). Si ces conditions ne sont pas satisfaites (Ms et Mf trop basses) un traitement par le froid pourra être envisagé pour transformer l’austénite résiduelle en martensite (Ms ne doit pas alors descendre au dessous de 250 °C environ).
Si l’épaisseur de la couche durcie doit dépasser 2 à 3 mm, il est nécessaire de mettre en œuvre un acier un peu trempant et donc légèrement allié.
La dureté de la couche durcie ne doit pas être affectée par un processus d’auto-revenu ce qui conduit ici encore à viser une température Mf voisine de la température ambiante (et à prolonger le refroidissement par la douche jusqu’à ce que la température à cœur soit au niveau de la température ambiante).
Pour assurer un bon soutient de la couche durcie l’acier doit permettre, si nécessaire, un traitement préalable dans la masse qui lui confère la tenue mécanique suffisante. Ce résultat peut être acquis à la suite d’une transformation bainitique ou d’une transformation martensitique (l’acier doit donc posséder la trempabilité nécessaire) suivie d’un revenu qui assure la stabilité structurale de la sous-couche qui sera affectée par la chaleur lors de la trempe superficielle (ceci suppose ici une température de revenu supérieure à 600 °C environ).